The Secrets of the Best Root Cause Analysis
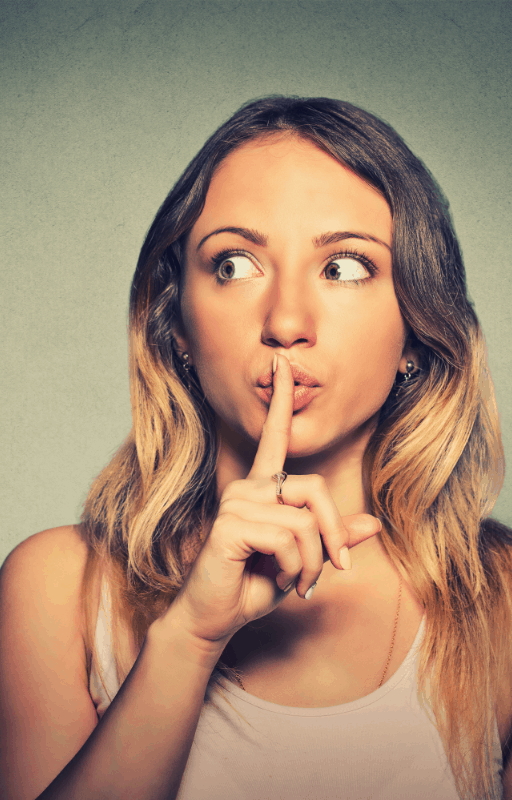
Root Cause Analysis . . .
Root Cause Analysis: Do you want effective root cause analysis? Do you want the BEST root cause analysis system?
If you want your root cause analysis to be effective (the best), you will want to learn about the seven secrets of effective root cause analysis that we have discovered from 35 years of research and development of the world’s best root cause analysis system.
The seven secrets of the best root cause analysis are:
- You have to understand what happened before you can understand the root causes.
- You must learn to interview and collect evidence.
- You won’t find THE root cause of an Incident.
- You need guidance to find root causes.
- You may want to go beyond root causes.
- You may need help developing effective fixes.
- Learning effective root cause analysis is easier and more fun than you might think.
That’s an interesting list. Read on to learn more…
But First, a Definition of Root Cause Analysis
However, before you can be the best and understand the secrets of effective root cause analysis, you need to define root cause analysis. The definition we have developed is:
ROOT CAUSE ANALYSIS
The process of finding the
missing best practices or
knowledge needed to prevent a problem.
This definition comes from a previous article (see THIS LINK) and from a series of books.
We’ve even made a video about the fundamentals of root cause analysis that you may want to watch before we review the secrets that you can use to make your root cause analysis the best…
What is the best way to make your root cause analysis effective? That’s an excellent question that frustrates many people. Below are the root cause analysis secrets that will help you achieve the best root cause analysis.
Root Cause Analysis Secret #1: You Have to Understand What Happened Before You Can Understand the Root Causes
That you first must understand what happened may seem obvious. However, many investigators, and some root cause tools, start by asking, “Why?” But for effective root cause analysis, you must start by understanding, “What happened?”
Starting by asking “Why” is jumping to conclusions. You are assuming you know what happened. It can lead to a problem called “Confirmation Bias.” You can read more about confirmation bias and the problems it can cause in a root cause analysis at THIS LINK.
But how do you fight confirmation bias? Our method starts by drawing a SnapCharT® Diagram of the facts you collect. Below is a simple SnapCharT® Diagram at the beginning of an investigation…

The SnapCharT® above outlines the famous 5-Why example that Taiichi Ohno (Toyota engineer) used. Here is how Taiichi Ohno describes it using a 5-Why root cause analysis:
1. Why did the robot stop?
The circuit has overloaded, causing a blown fuse.
2. Why did the circuit overload?
There was insufficient lubrication on the bearings, so they locked up.
3. Why was there insufficient lubrication on the bearings?
The oil pump on the robot is not circulating sufficient oil.
4. Why is the pump not circulating sufficient oil?
The pump intake is clogged with metal shavings.
5. Why is the intake clogged with metal shavings?
Because there is no filter on the pump.
For Mr. Ohno, that was the end of the root cause analysis. He said the root cause is no filter on the pump. Corrective action? Install a filter and get back to work. But this isn’t even the start of an effective root cause analysis.
We teach people to go beyond 5-Whys when performing a root cause analysis. We teach people to collect all the facts. Thus, a complete SnapCharT® Tahiichi Ohno’s example may look more like the SnapCharT® below…

If you would like to see a comparison of a 5-Why root cause analysis to an advanced root cause analysis system, see THIS LINK.
Root Cause Analysis Secret #2: You Must Learn How to Interview and Collect Evidence
To understand “What Happened?” you need to become an expert at interviewing people and collecting evidence. That includes learning:
- How to conduct investigative interviews using Cognitive Interviewing techniques in a 12-step process.
- To decode non-verbal behavior.
- To save your interview evidence on your SnapCharT®.
- To collect the 3 Ps and an R of evidence collection.
But where do you learn this evidence-collection and interviewing techniques? Try these courses:
- 5-Day TapRooT® Advanced Root Cause Analysis Team Leader Training (Live)
- 2-Day TapRooT® Evidence Collection & Interviewing Techniques Course (Live)
- How to Conduct Effective Interviews for Incident Investigations (Webinar)
- TapRooT® Evidence Collection & Investigative Interviewing Techniques (Online, Self-Guided, 3-Hour Training)
Or you can read THIS BOOK.

No matter which way you decide to learn, the techniques must help you perform better interviews and collect better evidence. The facts you discover will make your investigation fact-based rather than opinion-based.
Root Cause Analysis Secret #3: You Don’t Find THE Root Cause of an Incident
Some people think they need to find THE “root cause” (singular) of an incident. However, we discovered over 35 years ago that you need to identify the Incident’s Causal Factors and then find the root causes (plural) of each Causal Factor.
What is a Causal Factor? Here is a definition:
Causal Factor:
A mistake, error, or failure that directly leads to
(or causes) an Incident (the circle on the SnapCharT®) or
fails to mitigate the consequences of the original error.
We teach how to identify Causal Factors in our 2-Day, 3-Day Virtual, and 5-Day TapRooT® Courses.
Why is this secret so important? If you fail to identify all the problems that led to an Incident, you will fail to find all the root causes and fail to learn as much as you should about improving performance. Failure to learn and fix all the root causes allows problems to cause future incidents (or perhaps even more serious accidents).
Root Cause Analysis Secret #4: You Need Guidance to Find Root Causes
Most people don’t have years of training in human factors and don’t know why people make mistakes. Therefore, they assume that mistakes are due to carelessness. They think people need to try harder or be more careful.
However, the real root causes of human error are usually not someone else’s fault. They are due to shortcomings built into the system. If you fail to find and correct these shortcomings, the incident will continue to repeat (over and over again).
Therefore, people performing a root cause analysis need guidance to help them analyze human error-related root causes.
Learn more about guided root cause analysis at THIS LINK.
You may think that this guidance is only for inexperienced investigators. We have found that even experienced investigators need guidance to consistently find all the root causes. Watch the video below to find out why.
Root Cause Analysis Secret #5: You May Want to Go Beyond Root Causes
I thought the purpose of root cause analysis was to find and fix the incident’s root causes? Yes, it is. But you may want to learn more. For potentially high-complication incidents, you may want to find the generic causes that allowed the root causes to exist.
What is a Generic Cause?
Generic Cause
The systemic cause that allows a root cause to exist.
Fixing the Generic Cause eliminates whole classes of specific root causes.
If you find and fix Generic Causes, you will eliminate whole classes of root causes and see much more rapid performance improvement.
Root Cause Analysis Secret 6: You May Need Help Developing Effective Fixes
Over 25 years ago, we learned an important lesson. Even if people learn how to find root causes, they may not be able to develop effective corrective actions. Instead, they use the “standard” three corrective actions for every human error-related root cause. What are the standard three corrective actions?
- Training. If it didn’t work the first time, maybe more training would work.
- Discipline. This starts with counseling the person to be more careful. If that doesn’t work, use the progressive discipline system.
- Procedures. If you don’t have a procedure, write one. If you already have a procedure, make it longer!
Why do they always recommend these standard three corrective actions? Because that is what they always have seen in the past. And that is what management always approves.
Sometimes, they also use “Re” corrective actions. These include:
- Re-train
- Re-write the procedure (without specific guidance on what to change)
- Re-mind the operator about a rule or a way to do something
- Re-emphasize (same as reminding)
- Re-place a part (unless you have decided it was a Tolerable Failure)
- Re-evaluate (why wait – evaluate now and suggest a fix)
- Re-view (same as re-evaluate)
- Re-qualify (a variation on retrain)
- Re-peat anything (a warning, training, an evaluation, …)
If these actions didn’t work the first time, what makes you think they will work when you try them again?
How many of your corrective actions fall into the three standard corrective actions or a “Re” corrective action? Have you audited or evaluated your past corrective actions? Most facilities will find the percentage of ineffective corrective actions is way above 50%, perhaps as high as 90%.
How can you solve this problem of weak corrective actions? Use the TapRooT® Corrective Action Helper® Guide.

For every cause on the TapRooT® Root Cause Tree® Diagram, the Corrective Action Helper® Guide provides you with guidance to develop effective corrective actions.
It starts by having the investigator check that the root cause they are trying to fix is really a root cause for this incident. For example, for a “labels need improvement” root cause…

Next, the Corrective Action Helper® Guide provides “ideas” for correcting the root cause. For example, if you had a labeling problem…

Next, the Corrective Action Helper® Guide provides ideas for correcting Generic Causes…

Finally, The Corrective Action Helper® Guide provides references for the investigator to learn more about the problem…

That’s one example for one particular root cause. There are many more in the guide.
Where can you get the guide? The Corrective Action Helper® Guide comes with many of the TapRooT® Books and with TapRooT® Root Cause Analysis Training.
Root Cause Analysis Secret 7: Learning Effective Root Cause Analysis is Easier and More Fun Than You Might Think
The last secret is the secret way to learn all the previous secrets. We teach them in our TapRooT® Root Cause Analysis Training.
There are two 2-Day Courses that you may want to consider:
2-Day TapRooT® Root Cause Analysis Training
2-Day Equifactor® Equipment Troubleshooting
and TapRooT® Root Cause Analysis Training
Just click on the links above to see the course outlines.
Or you may want to attend the course that teaches all the TapRooT® Root Cause A\alysis Techniques … The 5-Day TapRooT® Advanced Root Cause Analysis Team Leader Training.
For upcoming public TapRooT® Root Cause Analysis Course dates and locations, see:
https://store.taproot.com/courses
It’s OK to spread the word about this secret root cause analysis training. You can even sponsor a course at your site to get all your investigators trained. Contact us for more information about scheduling a course at your site by CLICKING HERE.
Why would I say that a course about root cause analysis could be fun? Because so many students have told me so.
The student’s comment that I remember the best is…
When I canme to this course I wasn’t looking forward to it. My boss made me go. And let’s face it, most business courses are boring at best. But this course was fast paced. It had great exercises that really let us practice what we were learning. I really learned a lot. And probably the strangest part is … I had fun. This course wasn’t like a root canal (that I was dreading), it was great. I met interesting people and had a great time.
Get Started Making Your Root Cause Analysis Be the Best
If you haven’t attended a TapRooT® Root Cause Analysis Course, pick a course and register today.

If you have already attended a 2-Day TapRooT® Root Cause Analysis Course, call us to SAVE $500 when you register for the 5-Day TapRooT® Advanced Root Cause Analysis Team Leader Course.

Everyone should consider attending the Global TapRooT® Summit to learn the latest performance improvement methods.
