Are Your Corrective Actions Designed to Prevent Future Incidents?
I had a great conversation with one of our clients today. He mentioned that, with the price of oil below $50/barrel, his company is being proactive and looking at ways to improve their processes. One thing that they’re doing is reviewing old incidents and seeing where the commonalities lie. One item of interest that they found: They have discovered several instances of repeat problems. They found root causes, but they seem to pop up again.
What they are doing is what we call a Generic Cause analysis. They are looking deeper at their data and finding opportunities for improvement.
A review of the corrective actions found quite a few that seemed to be more akin to immediate actions than corrective actions. For example, if there was a production shutdown that was caused by a failed valve, the corrective action was, “Remove and repair the faulty valve.” Now, I’m not saying that this is necessarily a bad idea. However, is this corrective action aimed at preventing future recurrence of the incident? This corrective action, by itself, is designed more to restore plant operation, not prevent future issues.
Remarkably, this turned out to be more a terminology issue than a failure of their system. When asked about this, the Corrective Action team said, “Oh, you want actions that will prevent the incident in the future? Then you aren’t asking for ‘corrective actions’; you are asking for ‘preventative actions.’ You have to be clear what you want.”
TapRooT® does not really distinguish between these types of fixes. We expect all of these actions to be developed. We find that the “corrective actions” noted above are designed to fix the Causal Factor (“Valve failed to open. Therefore, repair the valve.”). This is as far as most other “root cause analysis” systems go, since they normally only get to the causal factor level.
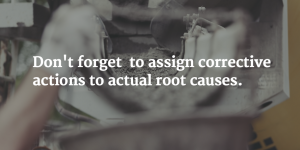
While you DO need to fix these issues, we also want you to continue to assign corrective actions to actual root causes. If the valve failed because the repair procedure specified the incorrect part (in TapRooT®, this root cause would be “facts wrong”), and you would therefore put a corrective action in place to fix this human-performance problem (“Update repair standard to indicate the correct gasket part number 885-33425”). This will fix not just this particular valve, but any valves in the future that are repaired using this same repair procedure. Without this corrective action, you will see this same issue pop up again as we continue to improperly repair valve failures.
Make sure you and your investigation teams are all on the same page. We use the term “Corrective Action” to indicate any and all actions that are designed to fix problems. Corrective Actions include those actions that fix the general issue (failed valve), and those that are designed to prevent the issue from occurring again in the future (procedure wrong). Take a look at your systems and make sure you are fixing both types of problems.
Sign up to receive tips like these in your inbox every Tuesday. Email Barb at editor@taproot.com and ask her to subscribe you to the TapRooT® Friends & Experts eNewsletter – a great resource for refreshing your TapRooT® skills and career development.