Analyzing Human Error with TapRooT® Root Cause Analysis
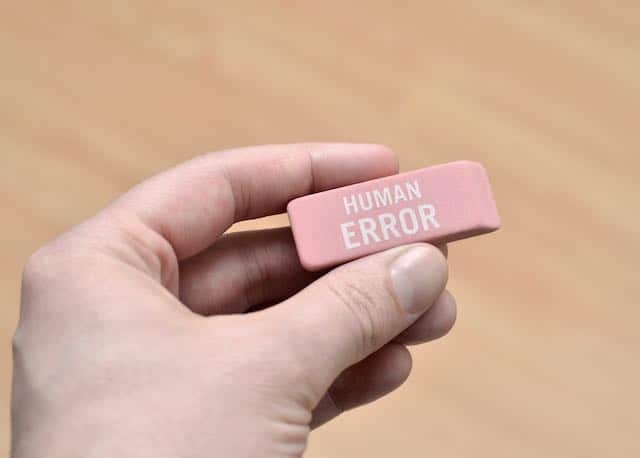
Analyzing Human Error with TapRooT® RCA – The History
The press frequently highlights the fact that accidents, incidents, quality problems, maintenance errors, medical errors, and many near-misses are due to human error. What does it take to improve human performance and stop human error? Advanced human performance technology. Analyzing human error was the original focus of TapRooT® and still is one of the biggest strengths of the TapRooT® System.

Mark Paradies teaching root cause analysis in the early 1990s.
Mark Paradies, one of the initial co-developers of the TapRooT® System, became familiar with advanced human factors technology during his studies at the University of Illinois. Mark had been in the Nuclear Navy for five years and was familiar with errors that operators and mechanics make even when they are well trained and have good procedures. His study of human performance taught him the theory behind human error and advanced concepts that could be applied to correct human factors problems. Ideas that go beyond procedures and training.
But these concepts and human factors theories aren’t very accessible to plant personnel, engineers, and managers (who were, in general, not trained in human factors). So, Mark decided to build the knowledge of human factors into the TapRooT® System without requiring advanced study to analyze human errors. This required careful design of the TapRooT® System to include advanced human performance technology without the jargon used by exeprts. What kind of advanced human performance technology did Linda Unger, the other prime developer, and Mark Paradies build into the TapRooT® System? Here are several of the sources:
1. The SOR Model of Human Performance
2. Rasmussen’s Skill-Rule-Knowledge Model of decision-making.
3. Advanced Job Performance Aids (procedures) practices.
4. The Systematic Approach to Training (SAT).
5. Application of Cockpit Resource Management.
6. Ergonomics (anthropometrics).
7. Team performance technology.
8. Communication reliability practices.
9. Short Term and Long Term Memory models and limitations.
10. Paradies’ Management System model.
11. Behavior-Based Safety models and practices.
12. Corrective Action Management best practices.
13. Audit and assessment best practices.
14. Employee management good practices.
15. Roscoe’s Display Principles.
16. Paul Fitt’s system concept.
17. Chris Wickens’ concepts on mental models.
18. James Reason’s Swiss Cheese Model of error.
19. Charles Hopkins’ concepts on human factors design.
20. Smoke Price’s concepts on automation and function allocation.
21. Paradies’ concepts on labeling and functional naming of equipment.
22. Advanced concepts on fatigue and alertness.
23. Advanced trending concepts.
24. Paradies’ and Unger’s model of human performance troubleshooting.
And the best part of TapRooT® is that this advanced human performance technology is invisible to the user. You don’t have to learn about all the concepts presented above, have a PhD in Psychology, or hire a human factors expert to take advantage of it to analyze a human error. You just answer the questions and follow the guidance that TapRooT® Root Cause Tree® Diagram provides to find the root causes of human performance errors.
Once the root causes have been identified, you then use the Corrective Action Helper® Module in the TapRooT® Software to help you develop effective fixes to human factors problems.
Unfortunately because this technology is invisible, some people don’t understand that it is there. They become convinced that they need a more complex, more difficult, harder to understand method to analyze human error. Some are even fooled that more basic human factors analysis concepts like Task Analysis or methods developed by engineers (Failure Modes and Effects Analysis, Hazop, or Fault Tree Analysis) that have been modified to analyze human performance problems are more advanced because they are harder to use. But difficulty in applying a tool does not mean that you will get better results.
Also, some have developed simplified models (that may seem complex) based on the Skill-Rule-Knowledge model initially developed by Rasmussen. These simplified systems put almost complete responsibility for improved performance on the operator, maintenance person, and supervisor. I often call these the “be careful” methods of human performance improvement.
Of course, being careful is good. But the methods miss some glaring opportunities for improvement because they focus so much of their human performance improvement effort trying to make people at the “sharp end of the stick” recognize error likely situations and then be careful when they are in one of those situations.
In our experience, neither the more difficult systems or the more simplified (but seemingly complex) ones produce better results than finding and fixing the root causes of human performance problems as accomplished by applying TapRooT® Root Cause Tree® when analyzing human errors.

The top of the Root Cause Tree® Diagram
Learning to Analyze Human Errors with TapRooT® RCA
The best way to learn to analyze human errors using TapRooT® Root Cause Analysis is our 5-Day TapRooT® Advanced Root Cause Analysis Team Leader Course. The course includes:
Course Outline
Day One (8:00 am to 5:00 pm)
- Class Introductions and TapRooT® Introduction
- TapRooT® System Overview – What You’ll Be Learning
- SnapCharT® Basics – Gathering Information
- SnapCharT® Exercise – Practice
- Causal Factors – Identifying the Errors
- Root Cause Tree® – Eliminating Blame
- Root Cause Tree® Exercise – On Your Own
- Corrective Actions – Developing Fixes
- Corrective Action Exercise
Day Two (8:00 am to 5:00 pm)
- Software Tips
- Generic Causes – Systemic Problems
- Enhanced Corrective Actions
- Preparing for Your Investigation
- Collecting Information
- Interviewing
- Interviewing Exercise
- Interviewing Exercise (RCA)
Day Three (8:00 am to 5:00 pm)
- Management System & Changing Behavior
- Equifactor®
- Human Engineering
- CHAP & Exercise
- Change Analysis
- Change Analysis Exercise
- Improving Procedures
- Putting It All Together
- Work Direction & Exercise
Day Four (8:00 am to 5:00 pm)
- Human Factors Jeopardy
- Proactive Improvement
- Auditing Using Safeguard Analysis
- Water Hammer Exercise
- Analyzing Training Problems
- Grading Investigations
- Presenting to Management
- Frequently Asked Questions
- Start Final Exercise (SnapCharT®)
Day Five (8:00 am to 1:00 pm)
- Final Exercise: Safeguards Analysis
- Final Exercise: Define Causal Factors
- Final Exercise: Find Root Causes
- Final Exercise: Find Generic Causes
- Final Exercise: Develop Fixes
- Final Exercise: Presentations
Course materials include:
- TapRooT® Essentials Book
- TapRooT® Major Investigations Book
- Laminated TapRooT® Root Cause Tree®
- TapRooT® Root Cause Tree® Dictionary
- Course Workbook
- Corrective Action Helper® Guide
Upon completion of the course, attendees will receive a certificate of completion and a 90-Day Subscription to TapRooT® Personal Software, our dynamic online software that guides you through the TapRooT® process with ease and efficiency.

Students learning to analyze human error.
You can register for one of our public 5-Day Courses from the courses at this link:
https://store.taproot.com/root-cause-analysis-advanced-team-leader
Or you can contact one of our TapRooT® Implementation Advisors (call 865-539-2139 or CLICK HERE) for a quote for training at your site.

TapRooT® Implementation Advisors
Going Beyond the 5-Day Course to Create a Human Performance Improvement Program
Analyzing human errors, accidents, quality problems, precursor incidents, and other issues by applying TapRooT® Root Cause Analysis is a good start on the way to excellent human performance. But investigating incidents is a reactive mode of improvement.
If you would like to also be PROACTIVE in improving human performance, you should attend our Stopping Human Error Training.
Here is what’s in the course:
Course Outline
Day 1 (10:00am to 6:00pm)
- Foundations of Improving Human Performance
- Human Performance – What Should You Expect?
- Three Human Reliability Best Practices
- Mistake Proofing
- Resilience
- Safeguards
- Using TapRooT® Root Cause Analysis for Reactive Problem Analysis
- Human Performance Improvement Technology (Catch Your Own Mistakes)
- STAR
- Questioning Attitude
- Attention to Detail
- Time Out
- Error Traps & Precursors
- Validate Assumptions
- Work Direction/Finding Error Likely Situations
- Pre-Job Hazard Analysis
- Pre-Job Brief
- Personal Safety Assessment
- Post-Job Brief
- Training
- Systematic Approach to Training
- Using Procedures to Improve Human Performance
- Procedures Best Practices
- Procedure Use and Adherence
- Place Keeping
Day 2 (10:00am to 6:00pm)
- Communications
- 3-Way Communication
- Do Not Disturb Sign
- Management System
- Conservative Decision Making
- Stopping Normalization of Deviation
- MOC
- Quality Control
- Independent Verification
- Concurrent Verification
- Human Factors Engineering
- Best Practices (Spot Bad Practices)
- Proactive Use of CHAP
- Hazard/Target Elimination or Substitution
- Improvement Exercise
- What Should You Improve/Which Tools Will Work Best for You?
- Sample Plan
- Present Your Plan (Benchmarking/Feedback)
With the exercises built-in to try the techniques, this is an active, quick-moving 2-day course.
You will leave this course with a clear understanding of methods to improve human performance and a custom plan to apply those methods at your company to achieve great gains in safety, quality, or operational and maintenance performance (all of which depend on human performance).

Alex Paradies teaching the Stopping Human Error Training.
Participants receive the book, Stopping Human Error, a $99.95 value, as part of the course materials. In addition, participants receive a certificate of completion and a 90-day subscription to TapRooT® VI Software, our dynamic cloud-based software that computerizes the TapRooT® Techniques.
The Best System to Analyze Human Error
We believe the TapRooT® Root Cause Analysis System and the Stopping Human Error Course are the best combination of reactive and proactive methods to improve human performance. If you are interested in advance human performance technology that can help you stop human error, learn the TapRooT® System and apply it to fix the root causes of human error.
As we mentioned previously, our courses are the best way to learn to anayze human error. However, if you would like to read more before attending one of our courses, here are some articles that might interest you…
Automation and Human Error
Is Human Error a Root Cause? (Updated)
Beyond Human Error as a Root Cause
Foreword of the New Book – Stopping Human Error – by Mark Paradies
Top 10 Wrong Ways to Stop Human Error