Pre-Job Hazard Analysis
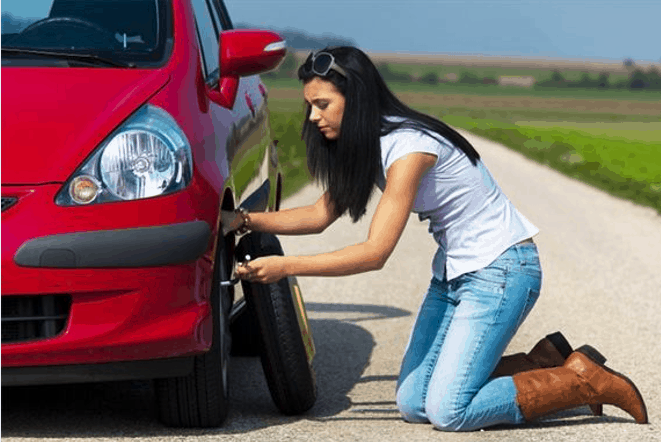
Be Proactive: Perform a Pre-Job Hazard Analysis
One of the four proactive tools in the Stopping Human Error book is Pre-Job Hazard Analysis.
Often these pre-job reviews go by other names:
- Job Safety Analysis
- Job Safety Assessment
- Pre-Task Hazard Analysis
- Job Hazard Analysis
- Task Safety Assessment
- Job Hazard Risk Assessment
- Activity Hazard Analysis
You would think that that’s enough names for the same thing but when they are performed by the worker they can be called a Personal Safety Assessment.
Usually, the assessment is performed by the supervisor.
How Do You Perform a JSA or JHA?
There are many processes taught in different courses but we teach a seven-step process in our Stopping Human Error Course. The seven steps are:
- Identify Hazards & Lessons Learned from previous jobs.
- Identify current Safeguards & strength of Safeguards.
- Are current Safeguards sufficient?
- Develop work permits, needed observations, and added Safeguards.
- Develop Pre-Job Brief to explain to workers:
- Hazards
- Safeguards (and their responsibility)
- PPE (and their responsibility)
- What to do if something unexpected occurs
- Supervise the work/audit. (When should supervisor be there?)
- Perform a Post-Job Review.
We included steps 6 and 7 because we didn’t think the work ended until the job was complete and reviewed.
Seems Easy But Actually Hard
Performing a JSA or JHA seems easy. But even a simple task, like changing a tire, can be difficult.
The first difficulty is spotting all the hazards. Why? Because some hazards are easier to spot than others.
For example, on the Energy Wheel below, what are the easiest Hazards to identify?
If you guessed Gravity and Motion, you are right. About 80% of the time or more these energy sources are identified. But what about the remaining energy sources? They get identified less than 50% of the time. (And sometimes much less than 50%.)
Would you like to learn how to improve the odds of identifying Hazards (Energy)? Then attend our Stopping Human Error Course in Knoxville, Tennessee, on September 15-16.
Stopping Human Error Training
What’s in the course? Here’s the course outline…
Course Outline
Day 1 (8:00am to 5:00pm)
- Foundations of Improving Human Performance
- Resilience and Safeguards
- Using TapRooT® Root Cause Analysis for Reactive Problem Analysis
- Using TapRooT® Human Performance Best Practices Proactively
- Human Engineering
- Procedures
- Training
- Communications
- Management System
- Work Direction
- Quality Control
- Stopping Normalization of Deviation
- Pre-Job Hazard Analysis
- Pre-Job Briefs
- Personal Safety Assessment
Day 2 (8:00am to 5:00pm)
- Applying Critical Human Action Profile Proactively
- Human Performance Improvement Technology
- Procedure Use/Adherence
- Place Keeping
- Independent Verification
- Three-Way Communication
- Pre-Job Brief
- Personal Safety Assessment
- Observation and Coaching
- Post-Job Brief
- Concurrent Verification
- Questioning Attitude
- Stop-Think-Act-Review
- Time Out
- Attention to Detail
- Management of Change
- Error Traps and Precursors
- Validate Assumptions
- Do Not Disturb Sign
- Conservative Decision Making
- Admiral Rickover and “Facing the Facts”
- Which Tools Will Work Best for You?
- Sample Plan/Suggested Plan
- Customizing Your Plan
- Present Your Plan, Benchmarking, and Feedback
With the exercises built-in to try the techniques, this is an active, quick-moving 2-day course.
You will leave this course with a clear understanding of methods to improve human performance and a custom plan to apply those methods at your company to achieve great gains in safety, quality, or operational and maintenance performance (all of which depend on human performance).
Participants receive the book, Stopping Human Error, a $99.95 value, as part of the course materials. In addition, participants receive a certificate of completion and a 90-day subscription to TapRooT® VI Software, our dynamic cloud-based software that computerizes the Equifactor® and TapRooT® Techniques.
So, if you are interested in learning about human performance and how to stop human error, you should be at this course. Still unsure? The course is GUARANTEED…
Attend this course, go back to work, and use the techniques you have learned to stop human error. If you don’t find new ways to improve human performance and if you and your management don’t agree that your efforts to improve human performance are much more effective, just return your course materials and we will refund the entire course fee.
To register for the Stopping Human Error Training on September 15-16 in Knoxville, Tennessee, CLICK HERE.