Fire Extinguished by a Questioning Attitude + Best Practices + Principles
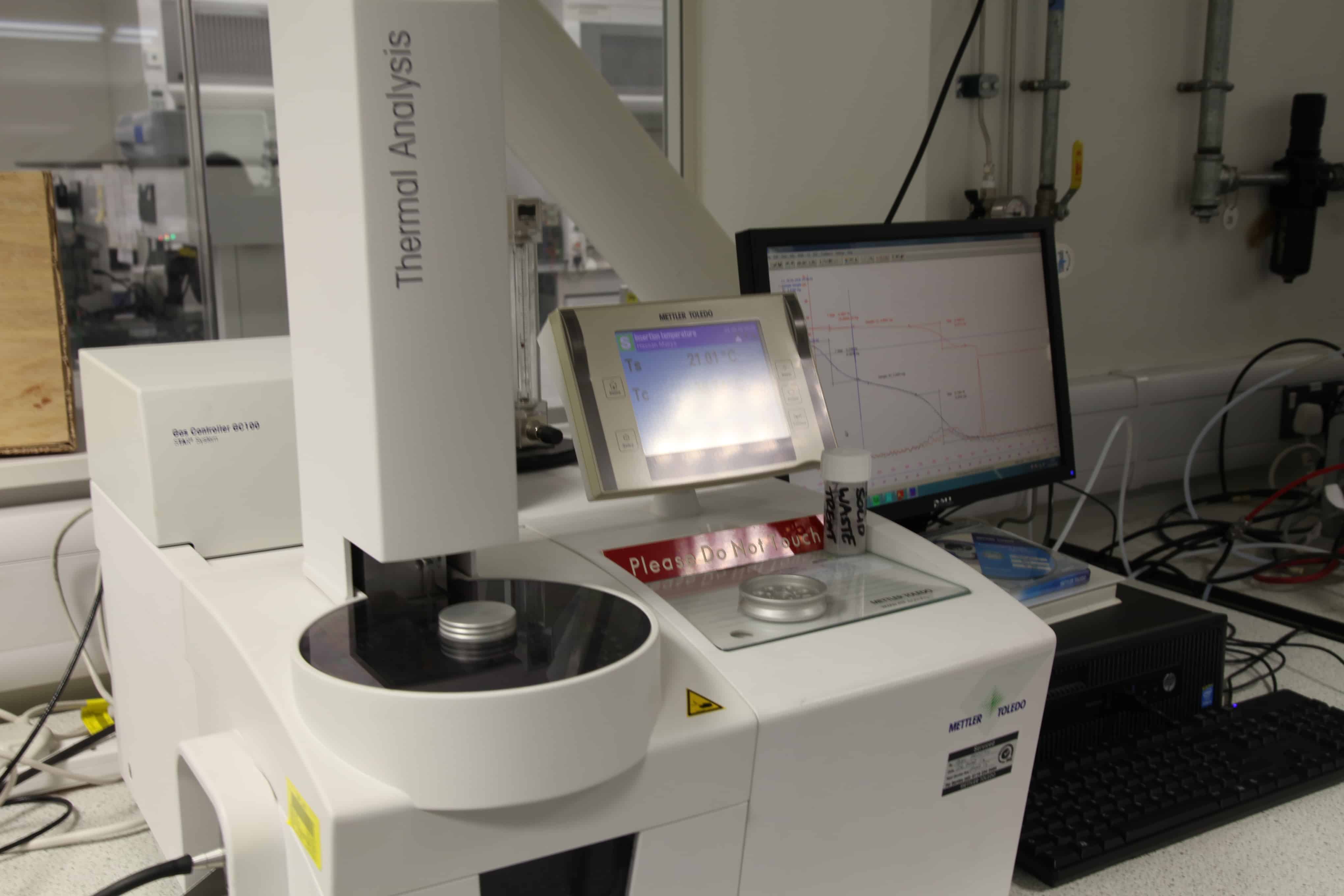
A researcher noticed an acrid odor and employed a questioning attitude, instinct, best practices, & principles to address a fire.
What would you do if you noticed a smell out of the ordinary but could write it off to electricians doing their work?
In January 2020, a Pacific Northwest National Laboratory (PNNL) researcher was pulling data from a Thermogravimetric Analyzer – Mass Spectrometry (TGA-MS) computer in a lab in the LSL2 building while electricians were replacing the lab’s light bulbs. The researcher noticed an acrid smell he attributed to the work the electricians were performing. However, because the smell was out of the ordinary, the researcher decided to check the heating elements on the TGA manifold. At that moment, the researcher heard a clicking sound coming from the water chiller used to cool the TGA manifold and then noticed sparks and small orange flames coming from the side grill of the chiller. He alerted the electricians, unplugged the chiller power cord and pulled the fire alarm, while the electricians called the PNNL Security Operations Center.
Although the fire extinguished itself once the power cord was unplugged, the Richland Fire Department arrived on the scene to assist in restoring the building back to normal service.
After the chiller was taken out of service, it was determined a hole had burned through the bottom of the chiller component. The chiller manufacturer later informed PNNL there were no recalls or any other concerns regarding this line of circulating chillers.
The PNNL staff response to this event could not have been any better.
- The researcher instinctively used the Safe Conduct of Research (SCoR) principles “A questioning attitude is cultivated” and “A healthy respect is maintained for what can go wrong” by questioning the source of the smell until it was located.
- The electricians’ immediate Single Point of Contact notification assured the fastest possible emergency response.
- In addition, the staff did not have any combustible material stored around the chiller; this is a PNNL best practice.
Lessons learned
• Staff should always be observant in a laboratory environment and never assume that off-normal events are correlated with normal activities.
• Staff should always deploy best practices in a laboratory environment as you just never know what could go wrong.
• Inspect all circulating chillers (Model AD 7L R-20) periodically for anomalies.
This Lessons Learned is from OPEXSHARE, U.S. Department of Energy. Published by Pacific Northwest National Laboratory (PNNL; Richland, Washington) 2/18/2020 “How SCoR Principles helped to extinguish the fire.”
Founded in 1988, the TapRooT® Root Cause Analysis System solves hurdles every investigator faces.
TapRooT® Root Cause Analysis Training System takes an investigator beyond his or her knowledge to think outside the box. Backed with extensive research in human performance, incident investigation, and root cause analysis, TapRooT® is a global leader in improved investigation effectiveness and productivity, stopping finger-pointing and blame, improving equipment reliability, and fixing operating problems.
System Improvements, the creator of the TapRooT® System, has a team of investigators and instructors with years of extensive training ready to offer assistance worldwide. We also offer ongoing support to our clients through free newsletters and root cause tip videos, the root cause analysis blog, and our annual Global TapRooT® Summit.
Register for a TapRooT® Course
Register for one of our TapRooT® courses. We offer a 2-Day TapRooT® Root Cause Analysis Course and a 5-Day TapRooT® Advanced Root Cause Analysis Team Leader Course. Contact us or call us at 865.539.2139 about having a course at your site or for further root cause analysis training opportunities. We’re here to help you find solutions.