The Importance of Management of Change with Risk Assessment
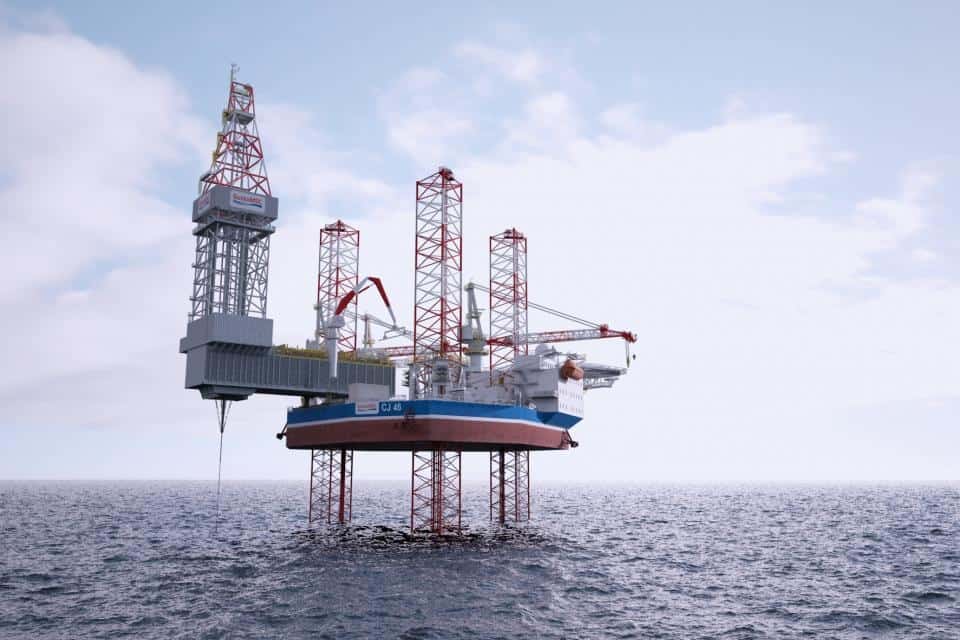
Know your barriers and management of change and risk in well control.
This well control incident highlights the importance of the management of change. It occurred on a jackup rig. On a development well, a sudden and strong flow through the tubing was experienced when the tubing hanger running tool (THRT), run on the landing string, was connected to the tubing hanger. This operation was being done in preparation for cutting the production tubing.
The well had BOPs (blowout preventers) installed; the reservoir was isolated with a deep-set bridge plug complete with cement dumped on top; and the TRSCSSV (Tubing Retrievable Surface Controlled Subsurface Safety Valve) was closed. When the THRT was connected, a sudden, strong flow through the tubing was experienced, and the string safety valve (FOSV) could not be installed. The well was only controlled when the blind shear rams were activated and the landing string was cut.
What went wrong with the well and the management of change?
A number of factors have been identified which contributed to the well control incident:
- The THRT was equipped with a “communication collar” which allows control line continuity above and below the tubing hanger whilst running completion. Although it is not proven, it is suspected that some pressure was applied to the control line during the make-up of the THRT which in turn opened the subsurface safety valve.
- The deep-set barrier of bridge plug with cement on top failed, hence, allowing communication with reservoir pressure.
- The tubing string contained well effluent (oil, gas, and brine) at the time of the incident.
Corrective actions and recommendations for well control incident and the management of change
- Importance of Management of Change (MOC) with risk assessment.
Two program steps were omitted but these changes were not evaluated through an MOC process. - A wait on cement period was programmed but not performed.
- An inflow test of the cement barrier was programmed but not performed. All barriers must be qualified, validated, monitored, and approved.
- A schematic of the well barrier envelope helps identify the critical elements, allowing discussion and visibility on how barriers have been tested and validated. A well barrier schematic was not utilized.
Content source and image credit: This Well Control Incident lesson sharing appears here courtesy of IOGP (International Association of Oil & Gas Producers), the voice of the global upstream oil and gas industry. IOGP members produce 40% of the world’s oil and gas. They operate in all producing regions: the Americas, Africa, Europe, the Middle East, the Caspian, Asia, and Australia.
The TapRooT® System trains you to solve problems – all types of problems
Circumstances can crop up in any occupation at any time if proper and safe sequence and procedures are not planned and followed. We encourage you to learn and use the TAPROOT® SYSTEM to solve problems.
TapRooT® has a team of investigators and instructors with years of extensive training ready to offer assistance worldwide. We also offer ongoing support to our clients through FREE NEWSLETTERS and ROOT CAUSE TIP VIDEOS, the ROOT CAUSE ANALYSIS BLOG, and our annual GLOBAL TAPROOT® SUMMIT.
Register for a TapRooT® Root Cause Analysis Training Course
Register for one of our TapRooT® Root Cause Analysis Training COURSES. We offer a basic 2-DAY COURSE and an advanced 5-DAY COURSE. CONTACT US. or call 865.539.2139 about having a course at your site or for further root cause analysis training opportunities. We’re here to find solutions for you.