Investigate Near Misses with TapRooT® Root Cause Analysis
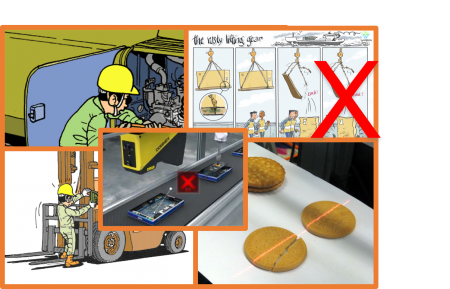
I think that TapRooT® Root Cause Analysis might be one of best way to investigate near misses, right?
I received this question from one my students who has continued to stay engaged to keep his company running safe and efficient by applying his TapRooT® Root Cause Analysis Training every day.
As you know, we are able to prevent real incidents by investigating near misses.
I think that TapRooT® RCA might be one of best ways to investigate near misses, right? Would you advise me how to use TapRooT RCA to investigate near misses and give me some examples of near miss investigations done with TapRooT® RCA?
Any comments or advice would be highly appreciated.
Think about it, in most near misses, you are just One Causal Factor from your next major Incident. The Causal Factors found during the investigation are usually not a surprise or the first time that they have occurred at that site or in the company.
The only difference between an incident and a near miss incident root cause analysis is what goes in the circle on the SnapCharT® (sequence of events chart). For example,
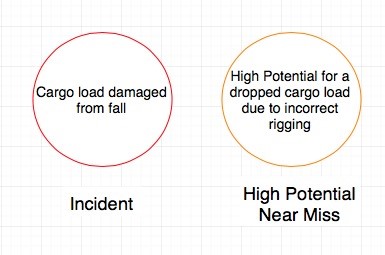
Vital to ensure success with a new near miss program implementation, is not to try to investigate all audit findings or catches. You do not have enough resources. Instead start with the high potentials for incidents only.
Wait, why did I just include audit findings? Simple, audits are more than looks for compliance. Processes are put in place to reduce or eliminate hazards (energy), isolate targets from hazards or to ensure responses to hazard and target contact do not make the incident worse. An audit is often the first documented point in time to identify a high potential near miss. Check out our new audit course with root cause analysis to improve your audit capability.
Just like I stated above concerning near misses, all audit findings may not need a root cause analysis, but audit findings with high potentials do.
If your company does not have a High Potential for Injury/Incident/Process Shutdown Program in place today, you will need to do some homework. Here are some simple steps to get started.
- Identify Tasks performed by your employees, contractors, vendors or suppliers, that if done incorrectly could cause Injury/Incident/Process Shutdown. For a jump start, review the following videos for Serious Injuries & Fatalities. For quality defects and process failures take a look at hierarchy of controls for defects.
- Once the potential tasks are identified, develop a triggering process that alerts the need for a root cause analysis.
Second homework item, if not trained in TapRooT® Root Cause Analysis, go to course close to you now.
If in Europe, check out our 5-Day TapRooT® Root Cause Analysis Course in Aberdeen, Scotland – May 22.
If in North America, checkout our 2-Day TapRooT® for Audits Charlotte, NC May 4, 2017 or our 5-Day TapRooT® Galveston, TX May 15, 2017.
Our complete course schedule can be found here.