Cutting the Incident Rate and Workers’ Compensation Costs with Advanced Root Cause Analysis
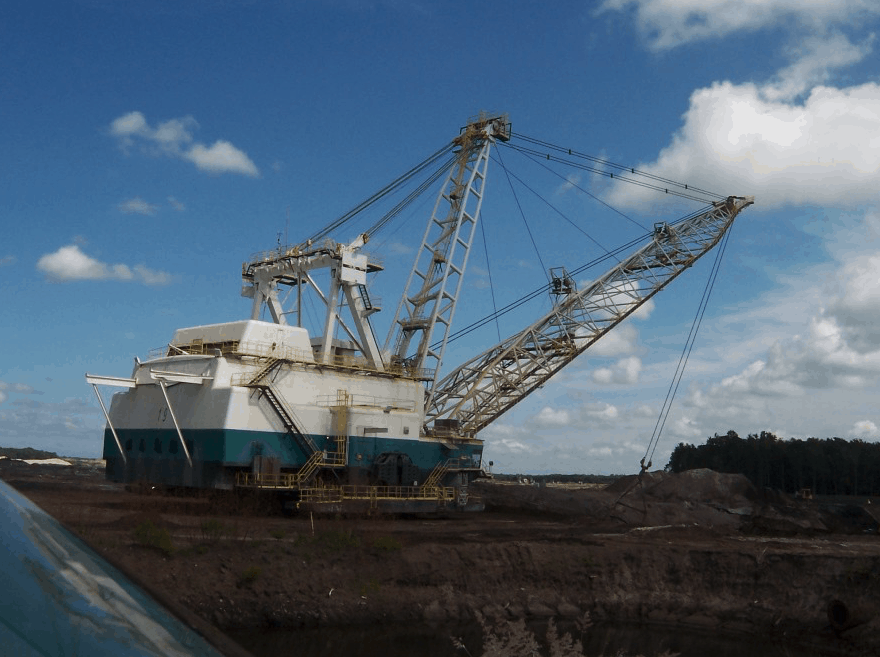
A TapRooT® User Success Story
Written by Larry Simmons
Safety & Health Manager
PCS Phosphate, White Springs
This success story was written in the past and is being updated to our most recent blog article format and is being reposted here.
Challenge
At our phosphate mining and chemical plants located in White Springs, Florida, we had been improving our safety processes throughout the ’80s and into the ’90s. We had recognized a need for improved consistency in our root cause analysis. With this in mind, I attended a 2-Day TapRooT® Root Cause Analysis Course in October of 1995 and was convinced that the TapRooT® System offered us the mechanism for improving our incident investigation system and ultimately achieving our goals in safety excellence.
Action
We began in 1996 by having System Improvements conduct two on-site 2-Day TapRooT® Root Cause Analysis Courses for 50 people (including frontline Supervisors, Superintendents, Safety Specialists, and our four Chief Shop Stewards from the union who serve as Safety Committee Chairmen). In addition, we held a four-hour overview class for our upper management including our Vice President of Operations.
We started by applying TapRooT® to analyze the root causes of our OSHA/MSHA recordable injuries and significant near-misses. As our confidence and experience with the system grew, root cause analysis and TapRooT® became “household words” for our employees and were used for a variety of analysis and improvement efforts. The TapRooT® Investigators were highly valued by management and employees. The acceptance of the TapRooT® System by our bargaining unit was an unanticipated benefit. This was at least partially due to the Chief Shop Stewards attending the same training as our Superintendents so that both groups had a clear understanding of the process and both could easily see that in TapRooT® there are no hidden agendas.
In 1997 and 1998, we have increased our skill in applying TapRooT and increased the scope of the investigations in which we apply TapRooT®. We now consistently apply TapRooT to all incidents including near-misses and first aid incidents. Looking for and fixing root causes for these smaller problems represents a paradigm shift for line management and employees alike. It also provides many more opportunities for our employees to hone their skills in the use of TapRooT®.
Results
Improvement in a single element of a safety process will normally not bring success for the total program. Also, increasing the number and scope of root cause investigations is only worthwhile if you can see results that justify the effort. However, we have seen a direct link between the improvements we have made to our incident investigation process by using TapRooT® and our total safety process results.
First, we have seen two improvements in our injury incident rate. Before implementing TapRooT our injury incident rate was 2.66. By 1997 it had declined to 1.75. After increasing our use of TapRooT to analyze near-misses and first aid incidents, our injury rate was cut in half (from our 1996 rate) to 1.27 for the first three quarters of 1998.
During the same period, we have achieved two safe work milestones for our site by working 1 million and 2 million hours consecutively without a lost-time accident.
These incident rate records have also led to financial rewards in the form of decreased workers’ compensation premiums that have more than paid for the cost of the TapRooT® Training.
Path Forward
Perhaps the best way to judge our belief in the effectiveness of the TapRooT System is to observe that we have licensed the use of the TapRooT® System and Software for our entire company.
(Note: Nutrien is still using TapRooT® to this day. Below is a more recent video success story as part of a 21st Century Business report.)