Using TapRooT® to Analyze Human Error
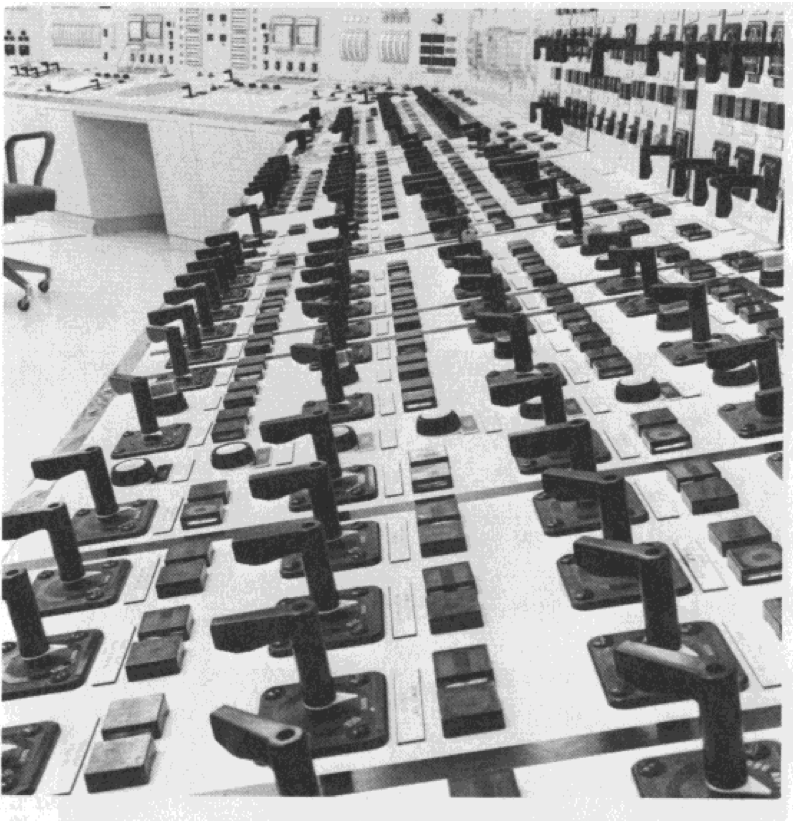
Advanced Human Performance Technology
The press frequently highlights the fact that accidents, incidents, quality problems, maintenance errors, medical errors, and many near-misses are due to human error. What does it take to improve human performance and stop human error? Advanced human performance technology.
Analyzing human performance was the original focus of TapRooT® and still is one of the biggest strengths of the TapRooT® System.
Mark Paradies, one of the initial co-developers of the TapRooT® System, became familiar with advanced human factors technology during his studies at the University of Illinois. Mark had been in the Nuclear Navy for five years and was familiar with errors that operators and mechanics make even when they are well trained and have good procedures. His study of human performance taught him the theory behind human error and advanced concepts that could be applied to correct human factors problems. But these concepts and human factors theories aren’t very accessible to plant personnel, engineers, and managers (who were, in general, not trained in human factors).
So Mark decided to build the knowledge of human factors into the TapRooT® System without requiring advanced study. This required careful design of the TapRooT® System to include advanced human performance technology without the jargon used by exeprts. What kind of advanced human performance technology did Linda Unger, the other prime developer, and he build into the TapRooT® System? Here is a sample:
1. The SOR Model of Human Performance
2. Rasmussen’s Skill-Rule-Knowledge Model of decision-making.
3. Advanced Job Performance Aids (procedures) practices.
4. The Systematic Approach to Training (SAT).
5. Application of Cockpit Resource Management.
6. Ergonomics (anthropometrics).
7. Team performance technology.
8. Communication reliability practices.
9. Short Term and Long Term Memory models and limitations.
10. Paradies’ Management System model.
11. Behavior-Based Safety models and practices.
12. Corrective Action Management best practices.
13. Audit and assessment best practices.
14. Employee management good practices.
15. Roscoe’s Display Principles.
16. Paul Fitt’s system concept.
17. Chris Wickens’ concepts on mental models.
18. James Reason’s Swiss Cheese Model of error.
19. Charles Hopkins’ concepts on human factors design.
20. Smoke Price’s concepts on automation and function allocation.
21. Paradies’ Concepts on labeling and Functional Naming of equipment.
22. Advanced concepts on fatigue and alertness.
23. Advanced trending concepts.
24. Paradies’ and Unger’s model of human performance troubleshooting.
And the best part of TapRooT® is that this advanced human performance technology is invisible to the user. You don’t have to learn about all the concepts presented above, have a PhD in Psychology, or hire a human factors expert to take advantage of it. You just answer the questions and follow the guidance that TapRooT® provides to find the root causes of human performance problems. Once the root causes have been identified, you then use the Corrective Action Helper® Module in the TapRooT® Software to help you develop effective fixes to human factors problems.
Unfortunately because this technology is invisible, some people become convinced that they need a more complex, more difficult, harder to understand method to analyze human error. Some are even fooled that more basic human factors analysis concepts like Task Analysis or methods developed by engineers (Failure Modes and Effects Analysis, Hazop, or Fault Tree Analysis) that have been modified to analyze human performance problems are more advanced because they are harder to use. But difficulty in applying a tool does not mean that you will get better results.
Also, some have developed simplified models (that may seem complex) based on the Skill-Rule-Knowledge model initially developed by Rasmussen. These simplified systems put almost complete responsibility for improved performance on the operator, maintenance person, and supervisor. I often call these the “be careful” methods of human performance improvement. Of course, being careful is good. But the methods miss some glaring opportunities for improvement because they focus so much of their human performance improvement effort trying to make people at the “sharp end of the stick” recognize error likely situations and then be careful when they are in one of those situations.
In our experience, neither the more difficult systems or the more simplified (but seemingly complex) ones produce better results than finding and fixing the root causes of human performance problems as accomplished by applying TapRooT®.
So if you are interested in advanced methods to analyze and prevent human error and you don’t mind that the techniques have been “human factored” to be easy to use ??? you should be using TapRooT®.
The best course to learn TapRooT® so that you can apply it to analyze human error is the 5-Day Advanced TapRooT® Investigator Team Leader Course. This course includes the TapRooT® Software (with the Corrective Action Helper® Module) and has many exercises that analyze simple and complex human errors.
So if you are interested in advance human performance technology that can help you stop human error, learn the TapRooT® System and apply it to fix the root causes of human error.
Read a paper about using TapRooT® to analyze a human error that causes an environmental release at a chemical plant at this link.