The Curse of Apparent Cause Analysis
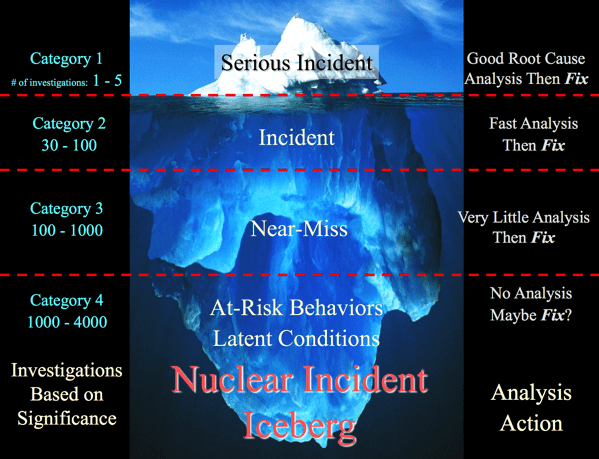
This Root Cause Network™ Newsletter article has received attention from many. Some have called me to praise the idea of more attention to serious incidents and proactive improvement. Others have questioned my views about NOT analyzing near-misses with “apparent cause analysis.”
Here is the article. Please add your comments by clicking on the comments link below.
The Curse of Apparent Cause Analysis
If you are not in the Nuclear Industry, you probably haven’t heard of Apparent Cause Analysis. If you are in the Nuclear Industry, you should wish that you never had. Why do I call Apparent Cause Analysis a curse while others say that it is a good practice? Read on to fully understand.
In almost every industry, the most frequent question asked by people that are doing good root cause analysis is:
Isn’t there an easier way to do this for smaller incidents?
That question led the Nuclear Industry to Apparent Cause Analysis. The idea is that you can skip some of the rigor of real root cause analysis, not ask as many questions, assume some facts, and even occasionally guess at the most likely cause and the result will be good enough to develop effective corrective actions and trends. Now for the bad news:
You get what you pay for.
When you take shortcuts, skimp on the facts, don’t ask all the questions, and guess, the result is a poor analysis that should NOT be used to develop corrective actions or to trend. Why? Because you will trend and correct the investigator’s assumptions and guesses. They may be good assumptions and guesses, but they may also be bad.
I tell people if saving time is their highest priority, why not use an even faster technique … Spin-a-Cause™!
“Implementing improvement based on our engineers’ best guess is better than doing nothing at all.”
My answer? NO, IT ISN’T!
Look at the iceberg model and think. A nuclear plant does 1 to 5 good root cause analyses per year. But they do 100s or even 1000s of short-cut analyses. The 1000s of corrective actions based on guesses & assumptions are driving their improvements. Is that why nuclear managers complain that improvement programs aren’t cost-effective?
So what should companies do? Here’s my advice:
1. Expand good root cause analysis to all incidents. (That’s about 100 incidents per year). It is cost-effective.
2. Learn to be efficient in your root cause analysis efforts without taking shortcuts. (Article on this is at the Root Cause Analysis Blog Site.)
3. Stop doing analysis on near misses and instead, categorize the occurrence types and watch for adverse trends.
4. Take the effort you save from not doing 1000 short-cut analyses and not fixing the assumed problems and put that effort into a targeted PROACTIVE improvement program based on good root cause analysis.
Need to learn more? Attend the 5-Day TapRooT® Course or talk to me at the TapRooT® Summit. But stop fooling yourself about getting something for nothing!