Use TapRooT® RCA to Improve an Existing Improvement Program
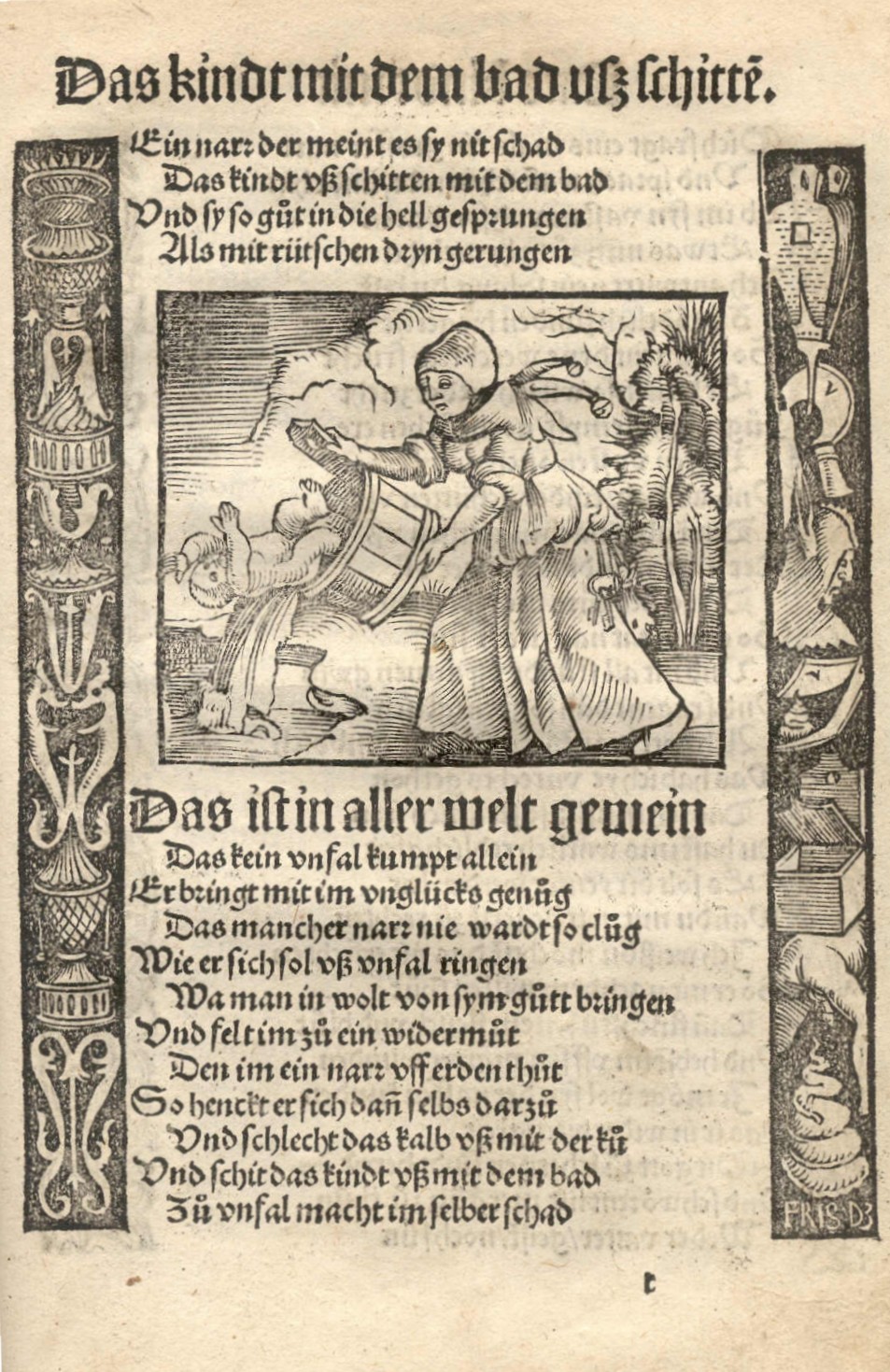
Improvements Not Making Progress
Has your improvement program stagnated? Have you been applying Lean or Six Sigma, and you think you need something more? Maybe your process safety improvement program has run out of gas? Maybe your Plan-Do Check-Act cycle isn’t working as it should.
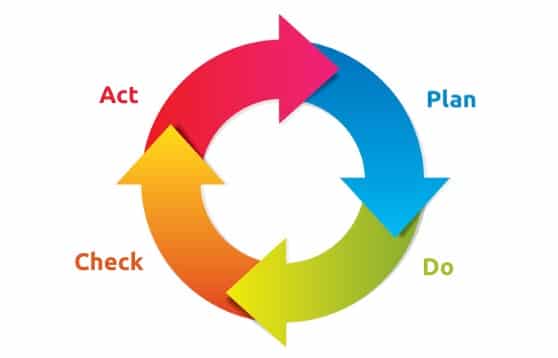
Don’t start all over. As they say…
Don’t throw the baby out with the bathwater!
(The earliest form of the quote above was in 1512 and included a woodcut illustration of a woman throwing out the baby with the bathwater – shown above. It was called an “Appeal to Fools.”)
What do you need? You need to improve your improvement program!
Easy Way to Improve Your Improvement Program
One problem almost any improvement program can experience is inadequate root cause analysis. Why? Because they usually include a simple but substandard form of root cause analysis. Examples of these simple but inadequate systems include:
- 5-Whys
- Fishbone Diagrams
- Cause-and-Effect
- Brainstorming
- Why Tree
I won’t go into the details of why these systems are inadequate but a few of the reasons include:
- Confirmation Bias
- Can’t go beyond current knowledge (especially for human error-related problems)
- Favorite Cause-itis
- Focusing on a single cause
So, one of the easiest ways to improve your improvement program is to adopt advanced root cause analysis – TapRooT® Root Cause Analysis!
For an example of how TapRooT® Root Cause Analysis goes beyond a simple technique like 5-Whys, see THIS ARTICLE.
How Does TapRooT® RCA Improve Your Improvement Efforts?
There are several ways that TapRooT® Root Cause Analysis improves your improvement efforts. They include:
- Finding the in-depth causes of human performance problems
- Better information collection
- Better equipment troubleshooting
- Improved corrective actions
And TapRooT® RCA accomplishes this improvement without being overly complex.
Let’s look at each of these ways that TapRooT® Root Cause Analysis can improve your improvement efforts…
Finding the In-Depth Causes of Human Performance Problems
TapRooT® Root Cause Analysis includes a root cause analysis tool called the Root Cause Tree® Diagram.
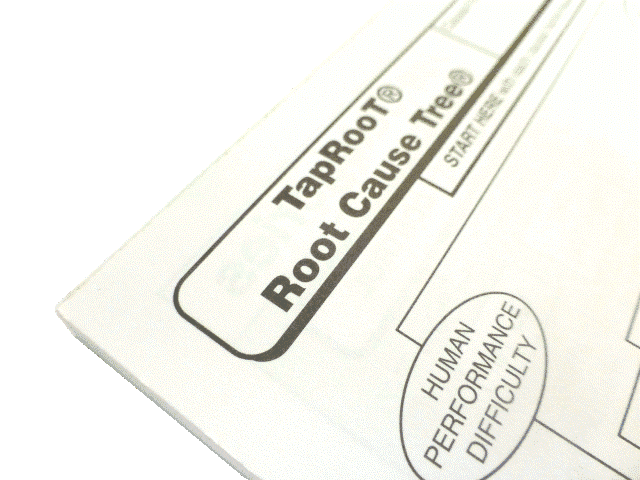
What does the Root Cause Tree® Diagram (and the Root Cause Tree® Dictionary) do to improve your root cause analysis? It guides the analyst to the true, fixable causes of human performance problems.
How does it do this? By using an easy-to-use tree of incident causation combined with a dictionary that defines all the terms used in the form of questions to be answered.
How do we know we have the right questions to guide an analyst? Simple … expert development, review, and testing.
Mark Paradies, Linda Unger, David Busch, and Dr. Paul Hass were among the initial developers. Their initial development was followed up by reviews by many human factors and root cause analysis experts, including:
- Dr. Charles O. Hopkins,
- Dr. Jens Rasmussen,
- Smoke Price,
- Dr. Alan Swain,
- Jerry Leaderer (first head of the forerunner of the NTSB),
- Larry Minnick,
- Heinz Bloch,
- Dr. Ann Ramey-Smith,
- Dr. Barclay Jones, and
- Dr. Joel Haight.
But the excellent development and reviews were just the start. There was extensive user testing. It started with reviews of hundreds of incidents to test the system. That was followed by field user testing by dozens of trained investigators. This was followed by reviews and suggested improvements by the TapRooT® Advisory Board (currently 62 TapRooT® Users from around the world).
The Root Cause Tree® Diagram, Dictionary, and training have been improved for 30+ years with feedback from hundreds of thousands of course attendees, and the improvement continues to this day.
For more about how the TapRooT® Root Cause Analysis System helps guide an investigation, CLICK HERE.
Better Information Collection
One of the features of the TapRooT® System that new TapRooT® Users especially appreciate is that it helps them understand what happened much more clearly. This is partly due to the better information they collect and organize into an understandable story of what happened. And you MUST understand what happened BEFORE you can understand why it happened.
How does TapRooT® RCA help investigators collect and organize their investigation information? With better information collection and organization tools, including:
- The SnapCharT® Diagram
- Change Analysis
- Critical Human Action Profile
I won’t explain all of these techniques and how they can be applied here, but you can see how some of the techniques are used in the environment incident example at THIS LINK.
Better Equipment Troubleshooting
Many incidents include equipment failures. Working with Heinz Bloch in the late 1990s, we discovered that many investigators, including equipment experts, weren’t thoroughly troubleshooting equipment problems before they started their root cause analysis. Therefore, we worked with Heinz to develop the Equifactor® Troubleshooting Tables and Technique to improve equipment troubleshooting, and we built the technique into the TapRooT® System.
The Equifactor® Troubleshooting Tables (a list provided below) provide expert troubleshooting guidance for pumps, compressors, fans, blowers, engines, electric motors, refrigeration units, conveyor belts, valves, bearings, gears, gear couplings, mechanical seals, and electrical components.

The guidance for troubleshooting a centrifugal pump with insufficient capacity is shown below.

In the case illustrated above, the troubleshooting result was the discovery that the pump’s impeller was installed backward. Many other causes were eliminated in the process of finding this problem.
These tables’ thoroughness and ease of use help investigators ask questions and gather the necessary information to understand how the equipment failed. That information helps the investigator continue the root cause analysis of why the equipment failed.
For more information about our Equifactor® Equipment Troubleshooting and TapRooT® Root Cause Analysis Training, CLICK HERE.
Improved Corrective Actions
Even with thorough root cause analysis, people may find it difficult to see outside-the-box corrective actions. Therefore, they continue to apply the same old corrective actions that didn’t work the last time…
- Training
- Discipline
- Procedures
We observed this limitation and developed the Corrective Action Helper® Guide to help people discover new, more effective ways to improve human performance and stop equipment failures.

The guide (built into the TapRooT® Software) helps investigators understand new ways to correct the root causes of problems. When it is combined with Safeguard Analysis and the Safeguard Hierarchy,

it can produce significant improvements in the effectiveness of corrective actions.
For more about developing better corrective actions see THIS LINK.
But There Is MORE! More Ways to Improve!
I know that what we have shared already may seem a little overwhelming, but when explained in one of our 2-Day, 3-Day, or 5-Day Courses (get more information HERE), even relatively inexperienced investigators get it.
And what do experienced investigators have to say? They wish they had learned these effective techniques way earlier in their career!
However, this isn’t all that there is to learn. In the early 1990s, we discovered that the root cause analysis and performance improvement landscape was always progressing. TapRooT® Users needed a way to keep up with the latest changes in:
- root cause analysis and incident investigation,
- human performance,
- equipment reliability and maintenance,
- high-reliability organization theory and best practices,
- safety and risk management,
- improvement program best practices,
- the psychology of improvement.
Therefore, we held the first Global TapRooT® Summit in 1994 and have held these Summits ever since.
These Summits are truly unparalleled ways to:
- Network with industry leaders,
- Learn and share best practices,
- Hear from amazing keynote speakers,
You must be at the next global TapRooT® Summit and discover how to take your improvement program to the next level.
What do prior attendees have to say?
- Pat, Suncor: “Fantastic speakers and sessions. I’m taking a lot of tools back to improve performance.”
- Teresa, Irving Oil: “The Summit was fun! There were wonderful speakers. I have a lot of good information to take back to my workplace.”
- Rich, PPL Electric Utilities: “Well organized. This was my first Summit and from the start to the end was a great experience and great networking.”
- Jeff, Halliburton: “It’s like a family reunion, except you meet root cause experts from around the world.”
- Dave, Marathon: “Very Valuable. Well-organized multiple breakout sessions with good practices and even some things not to do.”
- Jeff, First Energy: “This is my second Summit in a row, and each time I come, I learn new, valuable things to take back to work and apply,”
CLICK HERE to see the dates and location of the next Global TapRooT® Summit and learn more about why it is highly recommended by people interested in performance improvement.
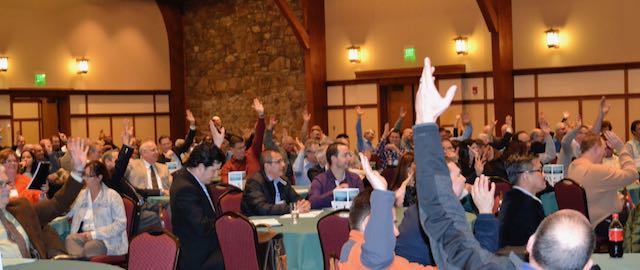
And CLICK HERE to register.