How To Analyze Maintenance Problems
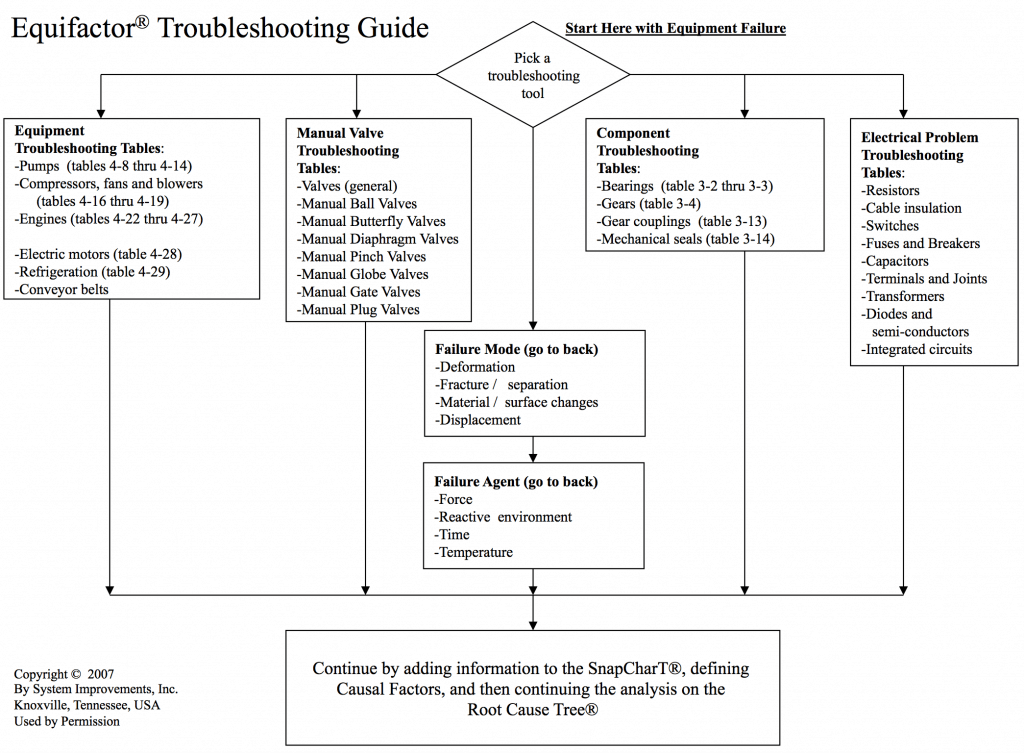
Do You Know How To Analyze Maintenance Problems?
Why Does the US Navy Have Serious Maintenance Issues?
Defense News reported that the US Navy has a serious maintenance issue. The article quotes a Navy document as saying:
Since fiscal year 2014, Navy ships have spent over 27,000 more days in maintenance than expected, with 70 percent of maintenance periods on average experiencing delays,
Sounds like they need effective root cause analysis to find the real root cause of these problems and implement effective fixes!
How To Analyze Maintenance Problems
First, a root cause analysis should be performed on every significant maintenance delay or ineffective maintenance performed. The data from these analyses could then be used to look for the Generic Causes of these problems.
But just any old root cause analysis isn’t good enough. These problems need effective, advanced root cause analysis – TapRooT®. And they need to use the Equifactor® Troubleshooting Tools that are unique to the TapRooT® System.
What is Equifactor®?
First, Equifactor is a set of troubleshooting tools built into a root cause analysis process. The process is outlined in the set of steps below…
The troubleshooting steps use Heinz Bloch’s troubleshooting tables and techniques (below).
Heinz is an equipment reliability expert that worked with System Improvements to develop the Equifactor® Troubleshooting System and build it into the TapRooT® Root Cause Analysis System.

Heinz Bloch – Equipment Reliability Expert
We licensed his knowledge and since 2007 have been working to seamlessly blend his techniques into the TapRoot® System and develop effective training to teach this advanced process to maintenance managers, equipment reliability engineers, field personnel who perform equipment troubleshooting, and incident investigators who don’t have extensive equipment troubleshooting experience. And we built Equifactor® Troubleshooting into the patented TapRooT® Software.
Where Can You Find Out More About Equifactor® and TapRooT®?
The first completely revised and improved Equifactor Troubleshooting and TapRooT® Root Cause Analysis Course is coming up on March 9-10. It is being held at the Horseshoe Bay Resort near Austin, TX. Ken Reed, a retired Nuclear Navy Master Chief and leader of the development of the Equifactor® Training will be one of the instructors for this course.
Get more course information here:
The next course is being held on March 9-10 at the Horseshoe Bay Resort near Austin, TX. This course is just before the 2020 Global TapRooT® Summit which also has a track on Achieving Excellence and Reliability.
If you attend the pre-Summit Equifactor® Course and the Summit you will save $200 off the combined Course/Summit price. Register for both the course and the Summit HERE.
Course Agenda and Materials
Here is the course agenda:
DAY ONE
- Introductions
- Understanding What Happened – SnapCharT® Basics
- SnapCharT® Exercise
- Collecting Information
- Failure Modes and Failure Agents
- Equifactor® Troubleshooting Tables
- Human Errors
- Process Troubleshooting
- Example: Troubleshooting a Seawater Pump
DAY TWO
- TapRooT®/Equifactor® Software Introduction
- Identifying Causal Factors
- Introduction to the Root Cause Tree®
- Exercise: Walking Through the Root Cause Tree®
- Exercise: Teams Find Root Causes Using the Root Cause Tree®
- Change Analysis
- Change Analysis Exercise
- Final Exercise: Solving a Major Equipment Issue
The course materials include the book, Using Equifactor® Troubleshooting Tools and TapRooT® Root Cause Analysis to Improve Equipment Reliability, a TapRooT® Root Cause Tree®, the Root Cause Tree® Dictionary, and the Corrective Action Helper® Guide, a $129 value. The book includes a complete set of Heinz Bloch’s troubleshooting tables.
Upon completion of the course, attendees will receive a certificate of completion and a 90-day subscription to TapRooT® VI Software, our dynamic cloud-based software that computerizes the Equifactor® and TapRooT® Techniques.
Course Guarantee
Attend this course, go back to work, and use what you have learned to analyze accidents, incidents, near-misses, equipment failures, operating issues, or quality problems. If you don’t find root causes that you previously would have overlooked and if you and your management don’t agree that the corrective actions that you recommend are much more effective, just return your course materials/software and we will refund the entire course fee.
Register TODAY!
A guaranteed course … what do you have to lose? This course has a limited number of seats. Reserve yours today by CLICKING HERE.