Avoid Food Recall with Root Cause Analysis
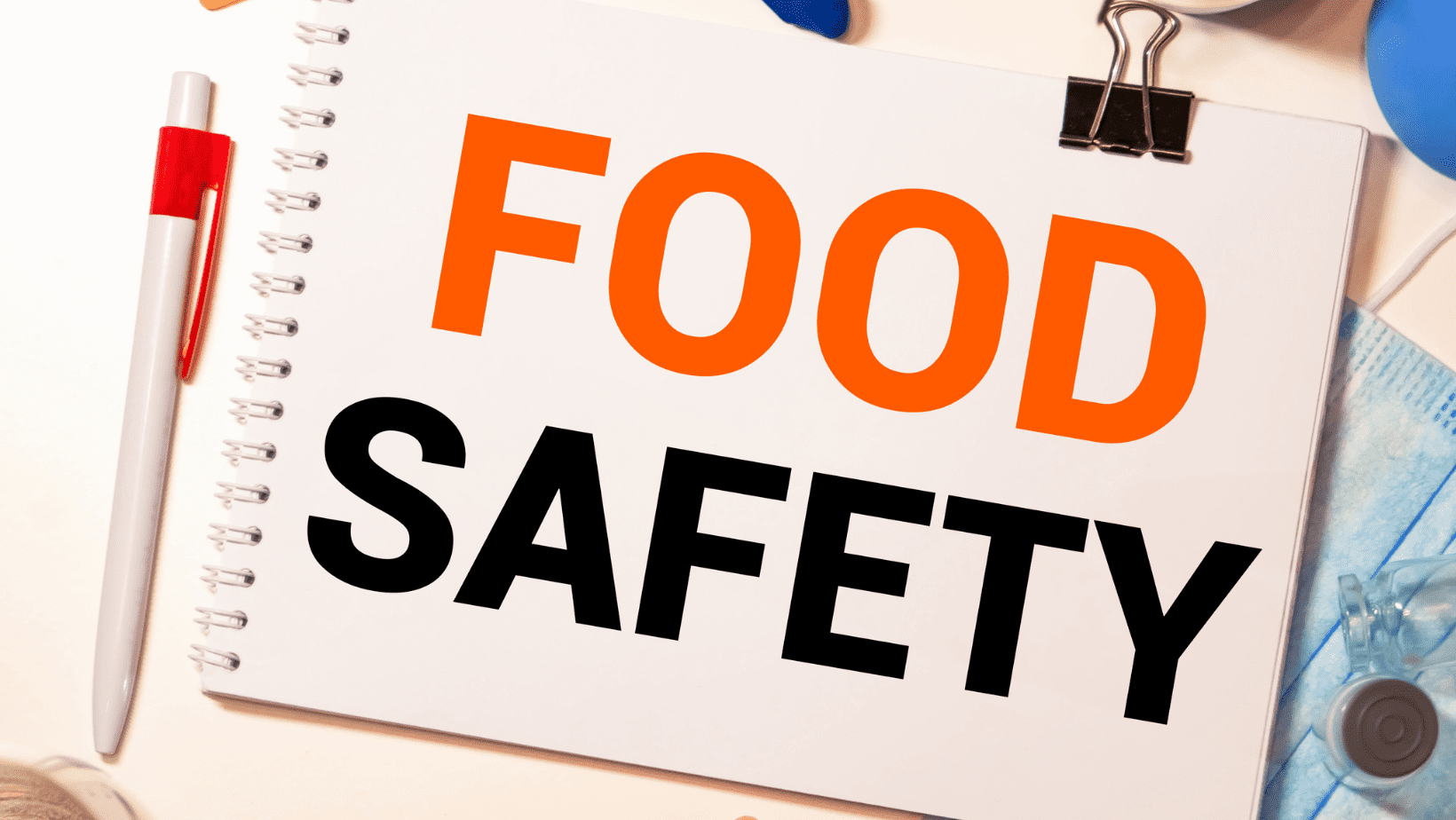
At my weekly grocery trip checkout, I was informed of a food recall on ground turkey I had purchased the week prior. The cashier was notified that something I purchased had been recalled, and the item detail printed on my receipt for reference. Per the article I found, the cause is listed as “extraneous materials, specifically blue plastic” as noted from consumer complaints.
An estimated 1 in 6 people get sick each year in the U.S. from foodborne diseases, according to the Centers for Disease Control and Prevention. Root cause analysis/incident investigation is an effective approach to fix accidents/incidents in the food industry.
Consider the TapRooT® Root Cause Analysis Process. It can be used proactively as well as reactively.
If you’re in the food and beverage industry, request a demo of the TapRooT® Process to show how the process guides you to the REAL root cause by contacting me at marambio@taproot.com. The demo will show you how TapRooT® goes beyond other systems as well as how to enact EFFECTIVE corrective actions so the incident does NOT repeat. Stop addressing the same issues over and over. Use TapRooT® to fix it for good.
Register today for a TapRooT® Root Cause Analysis Training Course (In-Person or Virtual) to Avoid a Food Recall
TapRooT® training is global to meet your needs. If you need particular times or locations, please see our full selection of courses.
System Improvements, Inc. | TapRooT® Root Cause Analysis was recognized as a top food safety solution provider by Food & Beverage Technology Review.
Learn more about what TapRooT® Root Cause Analysis offers to the Food & Beverage Industry.