CSB Recommends PSM Best Practices for Offshore Oil & Gas Corporate Boards
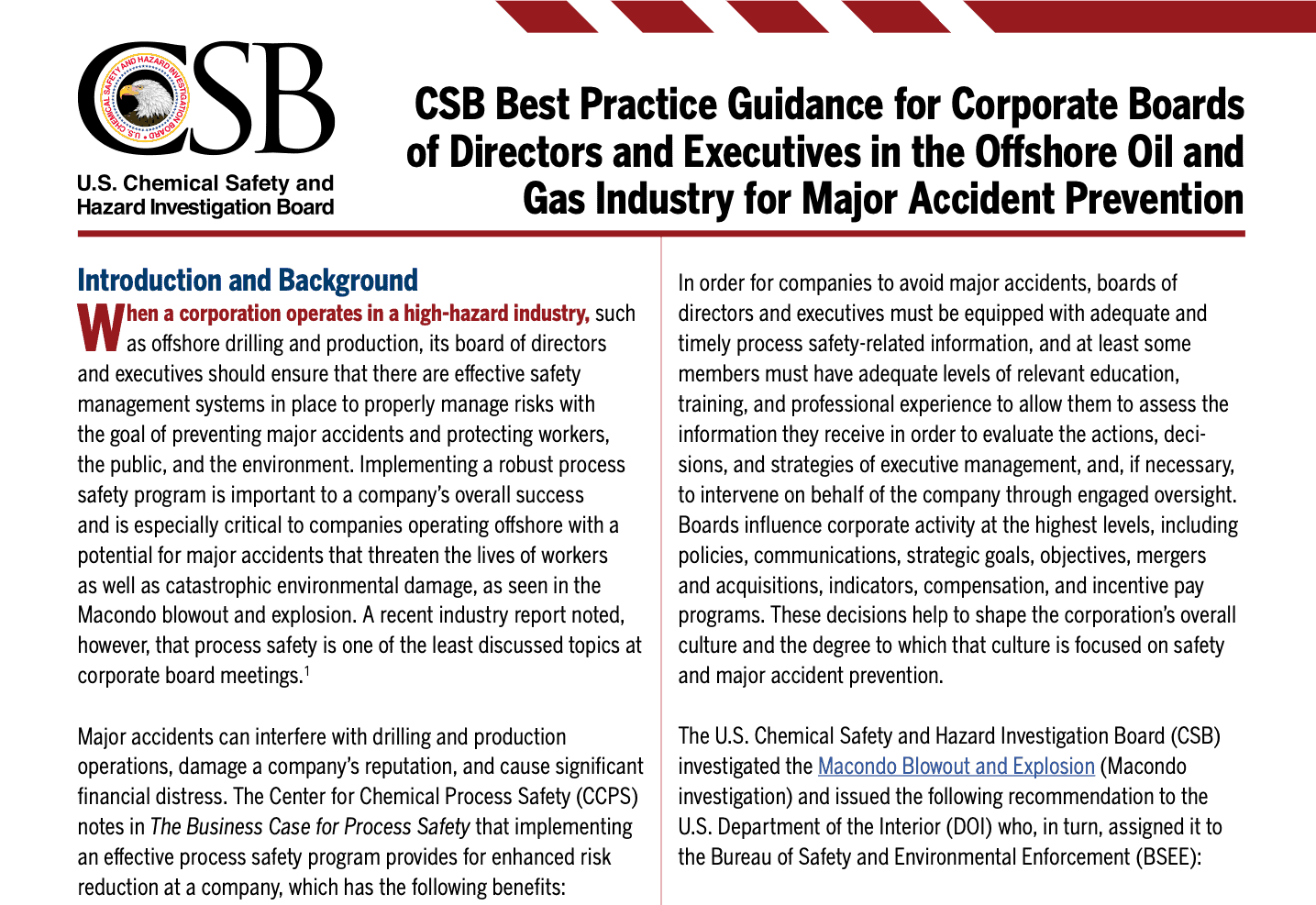
CSB PSM Recommendations for Offshore Companies Boards
Since the Deepwater Horizon (Macondo Well) accident, there have been many recommendations for better management of offshore drilling. Today, the US Chemical Safety Board (CSB) proposed additional guidance for Offshore Oil & Gas Corporate Board of Directors and references to previous guidance provided by industry associations and regulators. To download the guidance (a seven-page PDF), click on the link below…
https://www.csb.gov/assets/1/6/csb_macondo_bod_guidance_05_(1).pdf
I agree that senior management (the Board of Directors)of companies in high hazard industries need to have the knowledge and experience to guide the company including guiding their:
- process safety,
- aviation safety,
- nuclear safety. or
- drilling process safety
programs.
US Regulators, including:
- EPA,
- OSHA, and the
- BSEE
have already developed regulatory frameworks for process safety.
International regulators have also developed regulations that vary significantly from US regulations (for example, the Seveso Directive and Seveso Directive II). In addition, European regulators approved a directive for the offshore industry (European Offshore Directive (DIRECTIVE, 2013/30/EU),
All these regulatory directives and the additional guidance from professional societies (CCPS, API, CEFIC, …) provide extensive guidance for management. But they all seem to be missing essential elements that I recognize from my experience in the US Nuclear Navy.
Nuclear Navy Process Safety Guidance
The US Nuclear Navy was the first high-reliability organization. Some might say that it is still the ONLY high-reliability organization. Why would they say this? Because of the Nuclear navy’s safety record.
The first nuclear prototype (a functioning, land-based reactor), S1W, was completed in 1953. In 1955, the first nuclear-powered submarine, the USS Nautilus, got “Underway on Nuclear Power.” Both of these events were tremendous engineering accomplishments. But even more amazing was that Admiral Rickover, the father of the Nuclear Navy, created the management systems and culture that ensured that in the 67 years since the criticality of the first prototype, there have been no nuclear accidents (process safety accidents) in the Nuclear Navy. At its peak, the Nuclear Navy was operating over 100 reactors in a fleet of submarines, surface ships, and prototype reactors. What other industry can say they have achieved a perfect process safety record over that many operating units over that time period? I would suggest none. Not refining, oil and gas exploration, chemical plants, commercial nuclear plants, or even aviation.
Thus, I think the advice given by Admiral Rickover in Congressional Testimony should be referred to by anyone interested in achieving high-reliability and process safety.
That’s why I wrote a series of articles based on his congressional testimony. Here is a summary of the articles with links to each article…
No Such Thing as Normalization of Deviation
1. There is No Such Thing and the Normalization of Deviation
The point of this article is that deviation IS NORMAL. Management must do something SPECIAL to make deviation abnormal.
Stop Normalization of Deviation with Normalization of Excellence
2. Stop Normalization of Deviation with Normalization of Excellence
A brief history of how Admiral Rickover created the first high-performance organization – the Nuclear Navy.
The Nuclear Navy has a history of over 67 years of operating hundreds of reactors with ZERO reactor/nuclear (process) safety accidents.
He stopped the normalization of deviation with the NORMALIZATION OF EXCELLENCE. Excellence was the only standard that he would tolerate.
This article prepares readers for the three essential elements of his efforts to ensure reactor safety:
• Technical Competence
• Responsibility
• Facing the Facts
Each of these is detailed in the next three articles.
Technical Competency
3. Normalization of Excellence – The Rickover Legacy – Technical Competency
This article describes the first of Rickover’s three keys to nuclear (process) safety: TECHNICAL COMPETENCE. The big difference here is this isn’t just competence for operators or supervisors. Rickover required technical competence all the way to the CEO.
Responsibility
4. Normalization of Excellence – The Rickover Legacy – Responsibility
The second key to nuclear (process) safety excellence (the normalization of excellence) – RESPONSIBILITY.
Do you think you know what responsibility means? See what Rickover expected from himself, his staff, and everyone responsible for nuclear safety.
Facing the Facts
5. Normalization of Excellence – The Rickover Legacy – Facing the Facts
FACING THE FACTS is the most important of Rickover’s keys to achieving excellence.
Read examples from the Nuclear Navy and think about what your management does when there is a difficult decision to make.
Facing the facts could change your companies process safety management program.
18 Additional Elements of Rickover’s Approach
Here are the other 18 elements that Rickover said were required (in addition to the first three keys mentioned above).
That’s right, the keys are the start but you must do all of these 18 well.
Then read about the three problems that remained in the Nuclear Navy to completely achieve total performance excellence.
Rickover’s Congressional Testimony
Here is Rickover’s own writing on what makes the Nuclear Navy special. What to this day (over 35 years after Rickover was retired) keeps the reactor safety record spotless.
That’s it. The whole series. Hope you read every article.
Admiral Rickover Documentary Trailer
Missing Guidance
What’s Missing from Current Process Safety Management Guidance and Guidance for Corporate Boards? I think all three of Rickover’s main points outlined above:
- Facing the Facts
- Technical Competency (for management)
- Responsibility
are missing from current PSM guidance. You might have to read the articles above to understand what the three terms mean but, once you understand the terms and review how most companies run under process safety regulations are managed, you too will agree these critical elements aren’t required by the regulations and aren’t implemented in the oil or chemical industries.
Also, many companies are missing several (or many) of the 18 items listed in the “Other 18.” For example:
- Robust systems,
- Redundancy of equipment (to avoid shutdowns and emergency actions),
- Detailed preventative/predictive maintenance schedules strictly adhered to,
- Personal selection of leaders,
- Advanced training for higher leadership positions, and
- Strict enforcement of standards and disqualification for violations.
Without the implementation of these missing elements, industries running high-hazard facilities and offshore drilling platforms will never achieve the high-reliability performance achieved by the Nuclear Navy.
Nuclear Navy Wasn’t Perfect
In any organization, there is room for improvement. In my experience in the Nuclear Navy (be it 40 years ago), there was room for improvement that probably still needs improvement today. The three areas that needed improvement were:
- Blame Orientation (Lack of Praise)
- Fatigue
- Needed for Advanced Root Cause Analysis
Let me talk about each briefly.
Blame Orientation
The dark side of a high degree of responsibility was a tendency to blame the individual when something went wrong. Also, success wasn’t celebrated, it was expected. The result was burnout and attitude problems. This led to a fairly high turnover rate among the junior leaders and enlisted sailors.
Fatigue
Want to work long hours? Join the Nuclear Navy! Eighteen hour days, seven days a week were normal when at sea. In port, three-section duty (a 24 hour day every third day) was normal. This meant that you NEVER got a full weekend. Many errors were made due to fatigue. I remember a sailor was almost killed performing electrical work because of actions that just didn’t make sense. He had no explanation for his errors (they were multiple) and he knew better because he was the person that trained everyone else. But he had been working for over 45 days straight (a minimum of 12 hours per day). Was he fatigued? It never showed up in the incident investigation.
Need for Advanced Root Cause Analysis
Root Cause Analysis in the Nuclear Navy is fairly basic. However, everyone I talk to thinks they are advanced – until they are trained in what real advanced root cause analysis is. The Nuclear Nany assigns smart people and hopes they will find good “permanent fixes” to problems. And this works … sometimes. The problem? The Nuke Navy doesn’t train sailors and officers on how to investigate human errors. That’s where advanced root cause analysis comes in. TapRooT® has an expert system that helps people find the root causes of human error and produce fixes that stop the problems.
Whenever I hire a Navy Nuke (someone who recently left the Nuclear Navy) to work at System Improvements, they always tell me they already know about root cause analysis because they did that “on the boat.” But when they take one of our courses, they realize that they really had so much to learn.
If you would like to learn more about advanced root cause analysis, see our course offerings:
Or sign up for our weekly newsletter:
And call us (865-539-2139) or Contact Us for help implementing standards that will take you beyond the current state of the art in process safety by adopting Admiral Rickover’s secrets.