Comparing 5-Whys with Advanced Root Cause Analysis
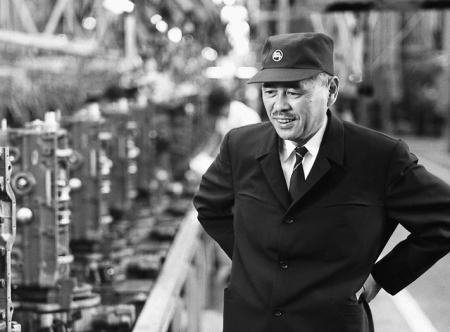
Comparing 5-Whys and Advanced RCA
I’ve heard people say that 5-Whys is a good root cause analysis system for “simple” incidents. Is it? Let’s compare 5-Whys using a simple incident that was provided as an example by a very experienced 5-Why user (Taiichi Ohno) to the same incident analyzed using the Advanced TapRooT® Root Cause Analysis System.
Read this article and you can judge the adequacy of 5-Whys for “simple” incidents.
5-Why Example
Taiichi Ohno, the father of the Toyota Production System and the creator of the 5-Why method of root cause analysis, is the source of the example – a robot failure. I’ve heard that he used the example to teach employees the 5-Why technique while he was at Toyota. Here is the 5-Why analysis as he described it…
1. Why did the robot stop?
– The circuit has overloaded, causing a blown fuse.
2. Why did the circuit overload?
– There was insufficient lubrication on the bearings, so they locked up.
3. Why was there insufficient lubrication on the bearings?
– The oil pump on the robot is not circulating sufficient oil.
4. Why is the pump not circulating sufficient oil?
– The pump intake is clogged with metal shavings.
5. Why is the intake clogged with metal shavings?
– Because there is no filter on the pump.
For Mr. Ohno, that was the end of the root cause process: Install a filter and get back to work.
Advanced Root Cause Analysis Example
Let’s look at this incident using the advanced root cause analysis and compare how 5-Why analyzed the problem to analysis using the TapRooT® Root Cause Analysis System.
The TapRooT® Root Cause Analysis Process
TapRooT® RCA is more than a tool. It is a systematic process with embedded tools to help an investigator find and fix the root causes of a problem. It starts with either the TapRooT® 5-Step Process for low-to-medium risk incidents or the TapRooT® 7-Step Process for major investigations. The 5-Step Process is shown below…

To start investigating the problem, one gathers evidence and draws a SnapCharT® Diagram (shown below being drawn using stickies by a team in a TapRooT® 2-Day Root Cause Analysis Course).
SnapCharT® Diagram
Notice that the 5-Whys that Mr. Ohno asked in the example above turned out to be mainly the sequence of events leading up to the failure in the SnapCharT® (shown below).
The SnapCharT® Diagram makes the example event easier to understand than the 5-Why example above. Plus, the SnapCharT® Diagram goes beyond the 5-Whys by indicating that there was no low oil pressure alarm.
In TapRooT® Root Cause Analysis, if the investigator decides that there is more to learn, the investigator continues to collect evidence (grows the SnapCharT® Diagram) to expand his/her understanding of what happened. A good TapRooT® Investigator would have several areas to review.
First, what happened to the filter? Was it forgotten during maintenance, or was it never designed into the system?
Next, where did the metal shavings come from? Metal shavings in a lube oil system are unusual. What was the source?
The new information provides a fairly complete understanding of what happened and is shown on the SnapCharT® below.

Notice that in the TapRooT® Root Cause Analysis System, we complete the collection of evidence about what caused the metal filings and what caused the filter to be missing. These are significant issues that were left out of the 5-Why analysis. This type of omission is common in 5-Why analyses – even when experts apply 5-Whys. Thus the problem isn’t with the investigator or their training – it is embedded in the 5-Why system.
Causal Factors
Once the investigator understands what happened, the third step is to identify the Causal Factors that, if eliminated, would have stopped the accident from occurring or reduce the seriousness of the incident. We use a Causal Factor Worksheet (not shown here) to identify the Causal Factors. The four Causal Factors for the Robot Stops incident were identified as:
- Mechanic A uses a cloth to cover openings in the system.
- Mechanic A does not report metal shaving contamination.
- Mechanic B does not install an oil filter.
- The operator does not know oil pressure is low.
Where Mr. Ohno only had one root cause, TapRooT® has already identified four Causal Factors. Each of these Causal Factors could have multiple root causes. This example highlights one of the weaknesses of 5-Whys: that it usually focuses on a single cause and misses additional causes (and the needed corrective actions for those causes that aren’t identified).
TapRooT® Root Cause Tree® Diagram
In the fourth step of the TapRooT® 5-Step Process, each Causal Factor is analyzed using the Root Cause Tree® Diagram to guide the investigator to the Causal Factor’s root causes. The tree is described in detail in the TapRooT® Book (CLICK HERE for info).
For this example, we won’t show the complete analysis of all four Causal Factors using the Root Cause Tree® and Dictionary.

For people who would like to know more about the 15-question Human Performance Troubleshooting Guide and the way the Root Cause Tree® Diagram is used to help investigators find causes beyond their current knowledge, we recommend attending a 2-Day or 5-Day TapRooT® Course.
However, we will describe the analysis of the Causal Factor “Operator doesn’t know oil pressure is low.”
This analysis starts on the Root Cause Tree® as a Human Performance Difficulty that leads us to the Human Performance Troubleshooting Guide.

Copyright © 2015 by System Improvements, Inc.
Used by permission. Duplication prohibited.
When asking the 15 Questions (a sample of the questions is shown above), two questions get a “yes” for this Causal Factor and guide us to the Human Engineering, Procedures, and Training Basic Cause Categories on the back side of the Root Cause Tree®.
Copyright © 2015 by System Improvements, Inc.
Used by permission. Duplication prohibited.
In analyzing these categories, no causes are found in the Procedures or Training Basic Cause Categories. However, two root causes are found to be applicable in the Human Engineering Basic Cause Category (above).
Thus, it was determined that if the operator needed an oil pressure display/alarm (displays NI root cause) to make the detection of a problem possible (errors not detectable root cause). If the display/alarm had been present, then the robot could have been stopped and fixed before damage to the bearings occurred. Thus, the incident would have been significantly less severe.
The corrective action for these two root causes would be to install a bearing lube oil pressure indicator and a low bearing lube oil pressure alarm to notify the operator of impending equipment problems before the bearing would lock up.
Our Conclusions: 5-Whys Compared
to the TapRooT® Root Cause Analysis
After analyzing just one Causal Factor using the TapRooT® Root Cause Tree® Diagram, we have found that even an expert like Taiichi Ohno could miss important root causes when using 5-Whys. But there is more. There are still three more Causal Factors to analyze (and then Generic Causes – an optional technique in the 5-Step Process).
So in conclusion, we asked…
- Why would someone use 5-Whys with these known, proven weaknesses?
- Why would someone risk lives, their corporate reputation, and large sums of money on an inferior approach to problem-solving?
The answer I hear is:
“It’s easy.”
But, my belief is, if something is worth fixing, it is worth fixing it right!
That’s why the sight amount of additional effort to collect all the relevant information and analyze it using TapRooT® Root Cause Analysis is worth the effort and actually SAVES TIME by fixing problems once and for all.
Therefore, I conclude that applying 5-Whys is a substandard solution. People who want to achieve excellence and save time and effort should be applying an advanced root cause analysis system – TapRooT®.
Would you like to learn more about the science behind why 5-Whys doesn’t work well? See these three articles:
Learn and apply TapRooT® Advanced Root Cause Analysis to find the real root causes of problems and effectively fix them. Attend an upcoming course to learn more.
For more details about how TapRooT® Root Cause Analysis works, download this white paper…

It seems to me there’s no way to find out there wasn’t an oil pressure gauge without asking, “Why didn’t the operator see the oil pressure was low?”
The fallacy in this article is the suggestion that “5 whys” has any special significance to the number 5. There was no significance to the number 5. It was just a number of “whys” one could expect to ask to come pretty close to the final root cause.
(Also, the point of “why” questions being sequential is that you don’t have enough information to ask the 2nd why until you had the answer to the 1st why. You don’t have enough information to ask the 5th why until you had answered the 4th why. It’s nothing but a systematic method of deductive reasoning. It’s such a tiny and simple technique, and so obvious, that it was always barely worth even mentioning.)
Thanks for your comment.
You could ask:
“How would the operationr know that the oil pressure is decreasing?”
Turning “whys” into “hows” is one of the things we teach in our evidence collection and interviewing course.
By the way, I’ve seen 17 whys not get to all the root causes. Mentioned that in the video attached to the article.