Almost every manager has been told not to micro-manage their direct reports. So the advice above:
Avoid Big Problems By Paying Attention to the Small Stuff
This may sound counter-intuitive.
Perhaps this quote from Admiral Rickover, leader of the most successful organization to implement process safety and organizational excellence, might make the concept clearer:
The Devil is in the details, but so is salvation.
When you talk to senior managers who existed through a major accident (the type that gets bad national press and results in a management shakeup), they never saw it coming.
A Senior VP at a utility told me:
It was like I was walking along on a bright sunny day and
the next thing I knew, I was at the bottom of a deep dark hole.
They never saw the accident coming. But they should have. And they should have prevented it. But HOW?
I have never seen a major accident that wasn’t preceded by precursor incidents.
What is a precursor incident?
A precursor incident is an incident that has low to moderate consequences but could have been much worse if …
- One or more Safeguards had failed
- It was a bad day (you were unlucky)
- You decided to cut costs just one more time and eliminated the hero that kept things from getting worse
- The sequence had changed just a little (the problem occurred on the night shift or other timing changed)
These types of incidents happen more often than people like to admit. Thus, they give management the opportunity to learn.
What is the response by most managers? Do they learn? NO. Why? Because the consequences of the little incidents are insignificant. Why waste valuable time, money, and resources investigating small consequence incidents? As one Plant Manager said:
If we investigated every incident, we would do nothing but investigate incidents.
Therefore, a quick and dirty root cause analysis is performed (think 5-Whys), and some easy corrective actions that really don’t change things that are implemented.
The result? It looks like the problem goes away. Why? Because big accidents usually have multiple Safeguards, and they seldom all fail at once. It’s sort of like James Reason’s Swiss Cheese Model…
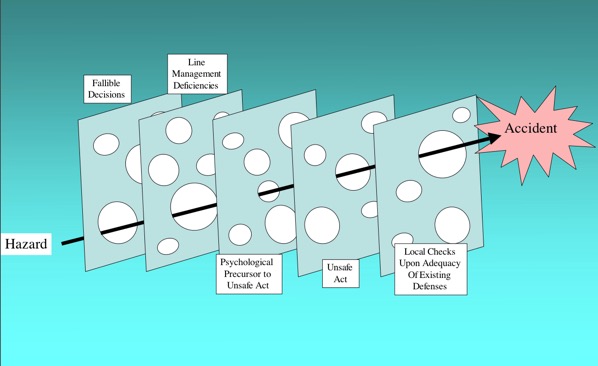
The holes move around and change size, but they don’t line up all the time. So, if you are lucky, you won’t be there when the accident happens. Maybe the small incidents repeat, but a big accident hasn’t happened (yet).
To prevent the accident, you need to learn from the small precursor incidents and fix the holes in the cheese or add additional Safeguards to prevent a major accident. The way you do this is by applying advanced root cause analysis to precursor incidents. Learn from the small stuff to avoid the big stuff. To avoid:
- Fatalities
- Serious injuries
- Major environmental releases
- Serious customer quality complaints
- Major process upsets and equipment failures
- Major project cost overruns
Admiral Rickover’s seventh rule (of seven) was:
The organization and members thereof must have the ability
and willingness to learn from mistakes of the past.
And the mistakes he referred to were both major accidents (which didn’t occur in the Nuclear Navy when it came to reactor safety) and precursor incidents.
Are you ready to learn from precursor incidents to avoid major accidents? Then stop trying to take shortcuts to save time and effort when investigating minor incidents (low actual consequences) that could have been worse. Start applying advanced root cause analysis to precursor incidents.
The first thing you will learn is that identifying the correct answer once is a whole lot easier than finding the wrong answer many times.
The second thing you will learn is that when people start finding the real root causes of problems and do real root cause analysis frequently, they get much better at problem-solving, and performance improves quickly. The effort required is less than doing many poor investigations.
Overall you will learn that the process pays for itself when advanced root cause analysis is applied consistently. Why? Because the “little stuff” that isn’t being fixed is much more costly than you think.
How do you get started?
The fastest way is by sending some folks to the 2-Day TapRooT® Root Cause Analysis Course to learn to investigate precursor incidents.
The 2-Day Course is a great start. But some of your best problem solvers need to learn more. They need the skills necessary to coach others to investigate significant incidents and major accidents. They need to attend the 5-Day TapRooT® Advanced Root Cause Analysis Team Leader Training.
Once you have the process started, you can develop a plan to improve your improvement efforts continually. Your organization will become willing to learn. You will prove how valuable these tools are and be willing to become the best in class.
Rome wasn’t built in a day, but you have to get started to see the progress you need to achieve. Start now and build on success.
Would you like to talk to one of our TapRooT® Experts to get even more ideas for improving your root cause analysis? Contact us by CLICKING HERE.
Keep in mind that people can’t do what they don’t know.
The can’t learn how to do RCA by Osmosis
It takes much more than reading this excellent article