GAO Calls for Root Cause Analysis of Cost Overruns & Schedule Delays on Columbia Class Submarines
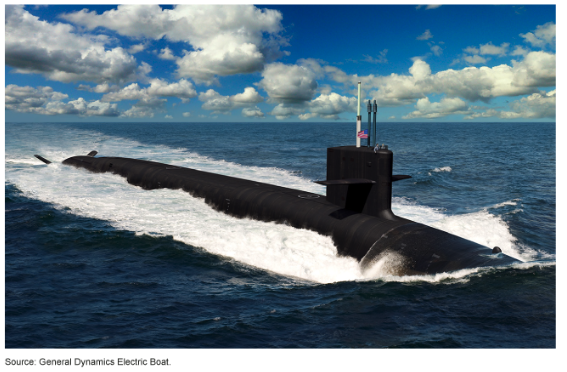
When Was the Last Major Military Procurement That Wasn’t Behind Schedule and Over Budget?
The new Columbia Class submarine is behind schedule and over budget. The GAO is projecting that these delays may make the new sub unavailable for deployment commitments in 2030 and, thus, impact military readiness.
To make matters worse, the GAO says even more schedule and cost problems could affect the other 11 submarines in the class if the root causes of delays and cost overruns are not understood and addressed.
GAO’s Recommendations
What are the GAO’s recommendations? There are five listed in the GAO’s press release:
- The Secretary of the Navy should ensure that the Deputy Commander for SUPSHIP has Electric Boat revise its cost estimate at completion to incorporate all remaining identified program risks and reflect likely levels of program performance based on historical trends.
- The Secretary of the Navy should ensure that the Deputy Commander for SUPSHIP, in conjunction with the Columbia class submarine program office, has Electric Boat produce EVM reporting that includes critical elements of variance analysis needed to better address future risks, such as an explanation of root cause, impacts to cost and schedule, and corrective actions.
- The Secretary of the Navy should ensure that the Columbia class submarine program, in conjunction with Electric Boat and Newport News, consistently identifies the information needed to determine whether production improvements and cost savings from supplier development funding are sufficiently supporting Columbia class construction goals.
- The Secretary of the Navy should ensure that the Deputy Commander for SUPSHIP has the SUPSHIPs Groton and Newport News update planning to ensure they have adequate resources and staffing needed to conduct quality assurance oversight of outsourced work at Electric Boat and Newport News strategic supplier facilities.
- The Secretary of the Navy should ensure that the Columbia class submarine program, in conjunction with the Deputy Commander for SUPSHIP, has Electric Boat update planning for submarine outsourcing, including expected hours and locations of outsourced work, to help SUPSHIP identify quality assurance oversight risks and request necessary resources.
CLICK HERE for the report’s highlights and links to the full report.
Inadequate Root Cause Analysis
Unfortunately, the GAO didn’t specify what “root cause” or “root cause analysis” meant. Therefore, the Deputy Commander for SUPSHIPS, the Columbia class program office, and Electric Boat may be applying substandard root cause analysis techniques like 5-Whys to analyze their problems.
What happens if you apply a substandard root cause analysis technique?
- Analysts stop before they reach the real root causes.
- Analysts jump to conclusions and only identify their “favorite” causes.
- Analysts find one root cause and fail to identify all the root causes, leaving problems undiscovered.
- Management doesn’t understand the true root causes that they need to address.
- Corrective actions for root causes are ineffective.
- People waste time implementing ineffective corrective actions.
- Problems continue. They don’t get solved.
To find out more about substandard root cause analysis and why it is substandard, read these articles:
- Under Scrutiny (Quality Progress – ASQ)
- What’s Fundamentally Wrong With 5-Whys?
- Comparing 5-Whys and Advanced Root Cause Analysis
- Get Real, Get Better
That should be enough reading to convince you that substandard root cause analysis is inadequate. But, if you would rather watch a video, watch this…
But what should you do to find the real root causes of serious problems needing effective corrective actions? (Things that you want to ensure never happen again.) Read on…
Advanced Root Cause Analysis
What is advanced root cause analysis and:
- Why does advanced root cause analysis find causes that 5-Whys misses and
- Why does advanced root cause analysis develop corrective actions that are much more effective?
First, advanced root cause analysis is TapRooT® Root Cause Analysis.
Why is TapRooT® Root Cause Analysis advanced? Because it meets all of these goals:
- Takes you beyond your current knowledge.
- Guides you to the fixable causes of human error.
- Expands the causes that you look for and are able to identify.
- Is repeatable.
- It is based on the evidence that you collect.
- It isn’t blame-oriented.
- Doesn’t contribute to hindsight bias or confirmation bias.
- It helps you develop corrective actions that stop repeat incidents.
The TapRooT® RCA System enables thorough, credible root cause analysis.
How did TapRooT® RCA become an advanced root cause analysis tool? Through careful design. TapRooT® Root Cause Analysis includes an expert system to analyze human error and advanced techniques for troubleshooting equipment problems. You can read about the history of the design of TapRooT® RCA HERE, the human factors knowledge that is embedded in the TapRooT® System HERE, and watch this video about the advanced equipment troubleshooting process…
Plus, the TapRooT® System has patented cloud-based software that makes the system even easier to use.
To see a white paper that explains the analysis of an environmental issue by using TapRooT® RCA, CLICK HERE.
The TapRooT® System even includes guidance for implementing a world-class root cause analysis program at your facility.
Don’t Hesitate – TapRooT® Training is Guaranteed
Don’t hesitate to try TapRooT® Root Cause Analysis and see what advanced root cause analysis can do for you. Why should you feel confident? Because TapRooT® RCA Training is guaranteed.
Here is our course guarantee:
Attend a TapRooT® RCA Course. Go back to work, and use what you have learned to analyze accidents, incidents, near-misses, equipment failures, operating issues, or quality problems. If you don’t find root causes that you previously would have overlooked and if you and your management don’t agree that the corrective actions that you recommend are much more effective, just return your course materials, and we will refund the entire course fee.
What course should you attend? See short course descriptions HERE.
What are the dates and locations of our upcoming public TapRooT® Courses? CLICK HERE to see the upcoming schedule.
Do you need a quote for a course at your site? Contact one of our Implementation Advisors by CLICKING HERE or by calling 865-539-2139.

Don’t wait! You can’t afford:
- Schedule slippage
- Cost overruns
- Lost time accidents
- Repeat equipment failures
- Quality issues
- Environmental accidents
You need to implement advanced root cause analysis NOW!