Equipment Wisdom: Gems from Heinz Bloch’s Petrochemical Machinery Insights
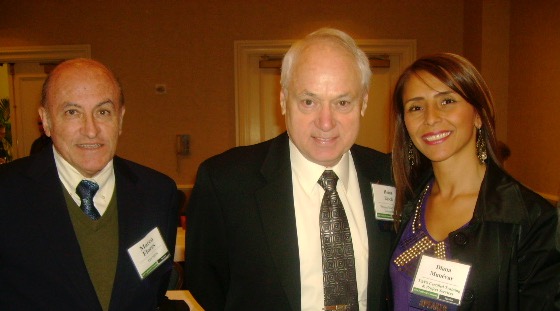
The late Heinz Bloch was a legend, a genius, and hilarious.
He wrote more scholarly articles than most of us have ever read (something like 760!!!).
I’ve been reading through his top three recommended books for getting smart fast from this podcast interview, and I wanted to start sharing some of his wisdom I’ve enjoyed.
Petrochemical Machinery Insights from Heinz Bloch
“I would like readers to consider a sobering definition: a mistake repeated more than once is called a decision.”
“By mistakenly accepting the notion that assets can be improved once the plant is running, the uninformed decision-makers frequently lock asset owners into a cycle of unprofitability and downtime risk. I liken this pathway to the foolishness of trying to turn a low-cost two-seater sports coupe into a safe and solid school bus. No amount of wishful thinking will let you do that in a profitable manner.”
“…tangible and lasting reliability improvements are achievable only if management and wage earners view every maintenance or downtime occurrence as an opportunity to find the true root cause.”
“Using oil rings and expecting the highest possible equipment reliability are contradictions. Attempts to live with contradictions (such as demanding the lowest price and expecting the highest reliability) will ultimately cost more than implementing best-available technology at the inception of a project.”
“Effective [Asset Management] deals with specifics. Not knowing these specifics and thus not implementing suitable upgrades will be very painful. The need for having a substantial amount of expertise will be ever more evident and is the common thread of this book…”
“…Working with the application groups of a reputable bearing manufacturer may simplify our life and greatly improve equipment reliability. The payback we get from making a solid bearing manufacturer our technology resource can be remarkable and is often expressed in weeks. … Cultivate access to this leader; shun those who are only selling bearings but cannot provide application know-how. Learn from their know-how; you will almost certainly have greater equipment availability and far fewer unscheduled downtime events.”
“As a general rule, responsible engineers at best-of-class companies see to it that cost estimating manuals reflect the outlay for uptime-optimized equipment. They verify their findings and disseminate all relevant information. Doing so will, at times, require standing up to the misguided folks who confuse the highly desirable sharing of knowledge with an illegal practice called restraint of trade. … Perhaps those who disagree with these sentiments might contemplate how they would fare if medical doctors refused to share with others the lessons they learned in practicing their skills!”
“Assigning the specifying engineering team to operations duties during and after commissioning allows companies to groom good engineers; it encourages them to investigate thoroughly and choose wisely. In short, their future career in project engineering and project management is linked to how well their first project performs in the two or three years after initial start-up.”
“Highly reliable manufacturers can compete because they keep scrap rates low. They keep their costs down by having infrequent warranty claims against them.”
Tie-rod assembled blowers are prone to failure. 2 years MTBF vs others with >20 years. See Dengyosha Machine Works (DMW).
“Vendors react to market forces, and traditional designs often win unless customers demand innovation.”

A few best practices that Heinz mentions:
- Invest in a laser alignment structure.
- Shaft-clamped oil flinger discs, oil mist, or jet oil systems. (Almost) Never oil rings.
- “Jet Oil lubrication is the only reliable solution for very high speeds and heavy loads” and yet “…[as of] 2015, unless the market demands it, pump manufacturers will not be offering this upgrade.” Easy advantage gain for the reliability-conscious engineer.
- Consider polyetheretherketone (PEEK) bearing cages as state-of-the-art.
Learn More of Heinz Bloch’s Wisdom
Learn more about Heinz Bloch’s wisdom. How? Attend a 2-Day Equifactor® Troubleshooting and TapRooT® Root Cause Analysis Course.
Heinz worked with us to develop the Equifactor® Troubleshooting Tables and Course. You need these advanced troubleshooting skills. Register HERE.
Also, you can learn even more at the Equipment Reliability Track at the next Global TapRooT® Summit.
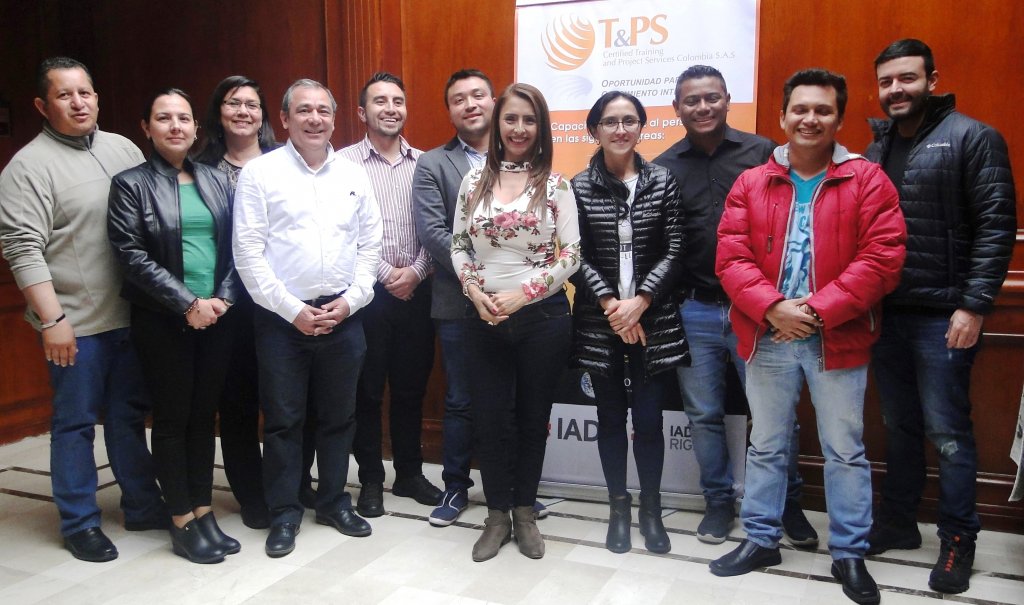
SAVE $300 OFF the course price when you attend BOTH the 2-Day Equifactor® Course and the Summit. CLICK HERE to register for both.
