Are You a “Serial Reactive”? (And getting absolutely nothing from it!)
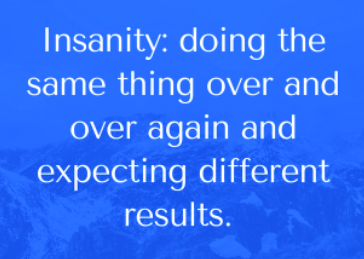
It seems to be a law of human nature — being a “serial reactive”: Stuck in a vicious cycle of wanting something fixed the moment it breaks.
As “serial reactives,” we immediately opt for the quickest fix available. Even if we acknowledge that this is but one in a repeating series of “this happened before and will happen again.”
Why do we keep choosing quick fixes at any cost — reactively throwing anything at the problem to prevent a disruption of the workflow? Especially if we know without doubt that the quick fix will fizzle out in pretty predictable short order.
How do you get past the routine of quick fixes, past the problem to a solution that works, past being a “serial reactive”?
We mean a solution that will keep on working. (Hint: If this sounds familiar, you can count yourself part of the problem — an a “serial reactive.”)
Imagine the downtime prevented and money saved NOT having repeat equipment failures. If this sounds interesting (and worthwhile), then this completely revised course is for you.
The Equifactor® Techniques are based on the work of noted equipment reliability expert Heinz Bloch.
In two days, you will learn how to use Equifactor® to troubleshoot equipment issues and find out what is leading to failures.
Then you will learn to use the TapRooT® System to organize the information you collect, identify the Causal Factors of the failure, and find the fixable root causes of the failure. Finally, you will learn to develop effective fixes to stop future equipment failures.
The tools you will learn include:
- Equifactor® Troubleshooting Tables – a systematic guide to troubleshooting common equipment problems.
- SnapCharT® Diagram – visualize and organize the information you collect to make what happened understandable.
- Root Cause Tree® Diagram and Dictionary – find the real, fixable root causes of human performance and equipment issues.
- Corrective Action Helper® Module – provides suggested corrective actions to help you develop effective fixes.
- Safeguard Analysis – helps define Causal Factors and develop effective corrective actions.
- Change Analysis – collect and understand information about problems caused by changes or differences in system, equipment, or people.
The tools can be used by maintenance personnel, equipment reliability specialists, maintenance managers, or investigators who don’t have an extensive understanding of equipment engineering.
In addition, the Equifactor® Techniques can be used to develop proactive equipment performance improvement initiatives and equipment troubleshooting procedures.
Course Outline
DAY ONE
- Introductions
- Understanding What Happened – SnapCharT® Basics
- SnapCharT® Exercise
- Collecting Information
- Failure Modes and Failure Agents
- Equifactor® Troubleshooting Tables
- Human Errors
- Process Troubleshooting
- Example: Troubleshooting a Seawater Pump
DAY TWO
- TapRooT®/Equifactor® Software Introduction
- Identifying Causal Factors
- Introduction to the Root Cause Tree®
- Exercise: Walking Through the Root Cause Tree®
- Exercise: Teams Find Root Causes Using the Root Cause Tree®
- Change Analysis
- Change Analysis Exercise
- Final Exercise: Solving a Major Equipment Issue
The course materials include the book, Using Equifactor® Troubleshooting Tools and TapRooT® Root Cause Analysis to Improve Equipment Reliability, a TapRooT® Root Cause Tree®, the Root Cause Tree® Dictionary, and the Corrective Action Helper® Guide, a $129 value. The book includes a complete set of Heinz Bloch’s troubleshooting tables.
Upon completion of the course, attendees will receive a certificate of completion and a 90-day subscription to TapRooT® VI Software, our dynamic cloud-based software that computerizes the Equifactor® and TapRooT® Techniques.
Don’t miss your opportunity to take an Equifactor course in May — and stop being a “serial reactive”
May 02, 2022 | 09:00 AM | EST | 2 Days | Equifactor® Equipment Troubleshooting & TapRooT® Root Cause Analysis | Knoxville, Tennessee |
Or check out the Equifactor® courses coming up (see link below). We will also teach Equifactor® at your site; just contact us to discuss. You may also call us for further information at 865. 539. 2139.