Rising Standards Mean You Need Advanced Root Cause Analysis Now!
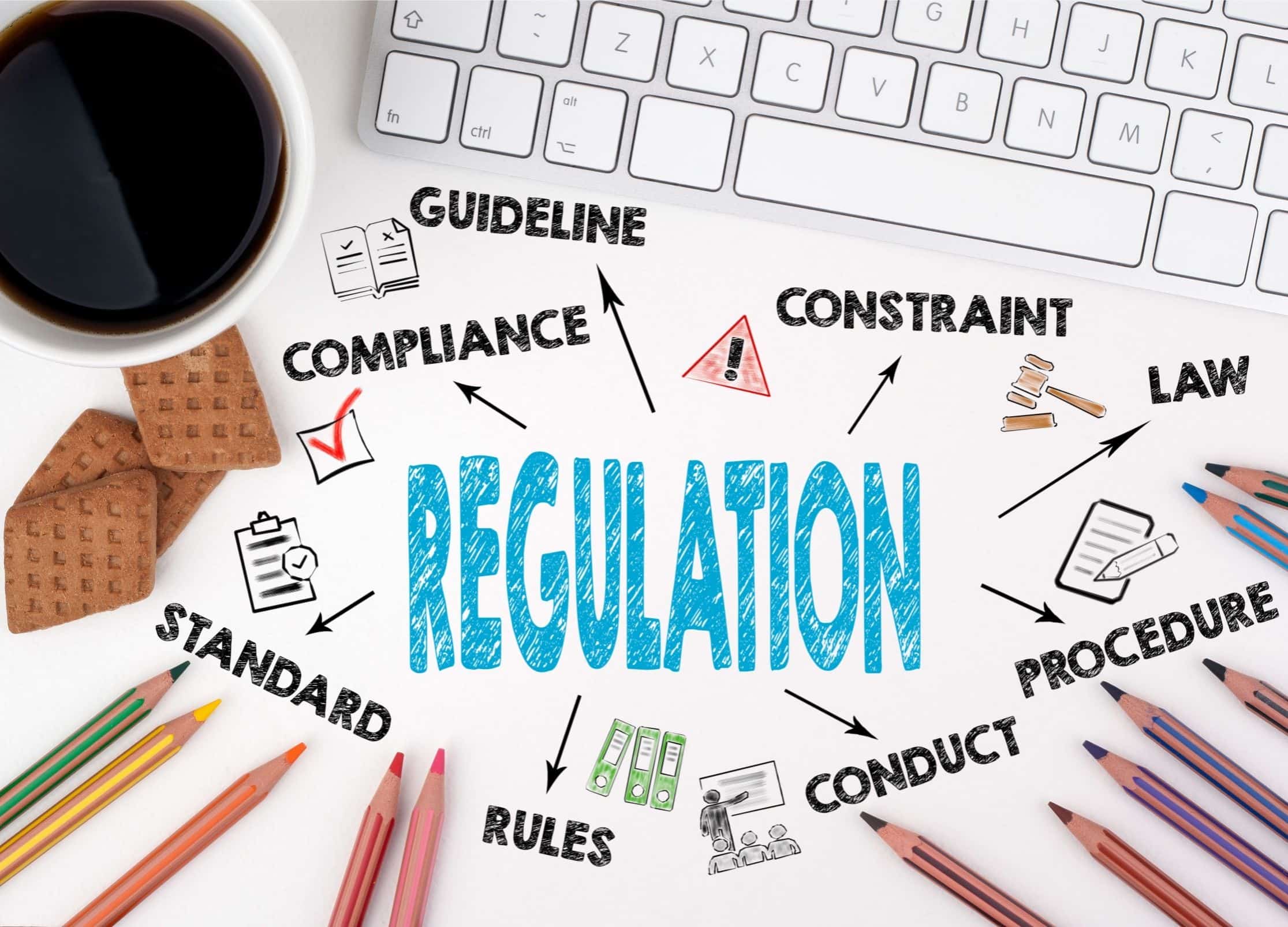
Rising Standards = Need for Advanced Root Cause Analysis
Rising Standards – Have you noticed how standards keep increasing?
- Regulators expect fewer accidental releases of pollutants.
- Management expects better performance at lower costs.
- Customers expect higher quality (or, perhaps, perfection).
- Normal human errors aren’t allowed (human perfection).
Everyone wants it better, cheaper, faster, and with less hassle and more service included than ever before. Errors aren’t acceptable. Performance must be perfect!
You might think of it as standards inflation!
Examples
- A refinery had a pipe failure that sprayed a mist of oil into the air and into the surrounding community. Thirty years ago, this would have been a minor incident. Now the regulator might shut down the facility as an imminent risk.
- Higher-priced labor in the USA might have been accepted by management as a cost of doing business in the 1970s. Now labor costs are compared to Asia, India, Mexico, or Eastern Europe. Or, worse yet, to the cost of automation. People might lose their jobs if productivity isn’t increased.
- A food contamination incident in the 1980s might have led to a recall and temporary removal of a product from the shelf. Now it results in a nationwide publicized recall, an FDA root cause analysis, facility shutdowns, loss of shelf space, negative publicity that will affect the company’s profitability for years to come, and in some cases … criminal prosecution of the company’s senior management.
What Should You Do?
Are you facing constantly increasing expectations from your management, your customers, or your regulators? Then you need to improve performance.
How can you get ahead and keep ahead? The answer is to apply advanced root cause analysis to improve learning from major or minor incidents reactively AND to improve based on a proactive continuous improvement applying the same root cause analysis techniques.
Read on to explore these ideas…
Reactive Improvement
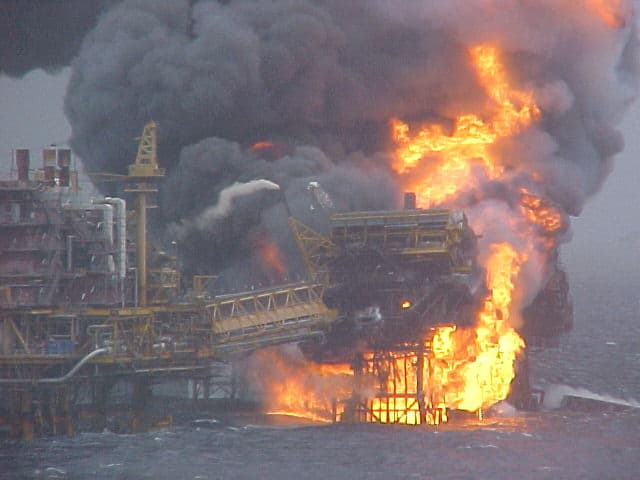
Everybody knows about reactive improvement. If you have an accident, an incident, an operating upset, or another problem, you investigate the root causes and implement improvements.
What’s the problem with this approach?
- You are waiting for something bad to happen to learn how to improve.
- Many people apply “simple” root cause analysis techniques that really don’t work well (5-Whys, Cause-and-Effect, Fishbone Diagrams, Checklists). How can you tell these techniques don’t work well? Repeat incidents.
- The “simple” techniques naturally lead to weak corrective actions like discipline, retraining, and longer procedures.
- The simple techniques don’t guide the investigators to troubleshoot equipment problems or find the causes of human error.
Thus, poor root cause analysis leads to failed reactive improvement. Accidents aren’t prevented, and management and regulators are left with little confidence that future performance will improve.
To be effective, companies need advanced root cause analysis. Root Cause analysis that solves problems 2-4 described above by accomplishing the fundamentals of advanced root cause analysis.
Proactive Improvement
The solution to problem #1 above – waiting for something bad to happen to improve – is to become PROACTIVE.
Great companies don’t wait for an accident to improve. They understand their risks and target the most serious risks with audits, assessments, observations, management walkarounds, and other continuous improvement initiatives to find and fix problems before accidents happen.
Also, they apply advanced root cause analysis to solve the problems they discover. This ensures effective corrective actions that stop repeat problems.
How can you learn more about applying advanced root cause analysis to proactively improve performance? EASY!

Attend the 2-Day Auditing & Proactive Improvement Using TapRooT® RCA Course being held on April 29-30 just before the 2024 Global TapRooT® Summit (May 1-3). The course and the Summit are being held near Austin, Texas, at the Horseshoe Bay Resort.

To find out more about the pre-Summit Courses and the Summit, CLICK HERE. I know the course isn’t until 2024, but don’t wait to register. These pre-Summit Courses have a limited number of seats and fill up. REGISTER today for the course and the Summit and SAVE $300 off the combined registration fee.

Advanced Root Cause Analysis for Incident Investigations
What is advanced root cause analysis?
First, it covers all the fundamentals of root cause analysis. Below are Mark Paradies and Benna Hughes discussing the fundamentals of root cause analysis…
Advanced root cause analysis helps you understand what happened BEFORE you start asking why it happened.
Second, an advanced root cause analysis system understands that most (all?) accidents, incidents, and problems discovered by reactive improvement (incident investigations) are caused by multiple causal factors. Each of these causal factors needs to be analyzed to find the causal factor’s root causes.
So, for each causal factor, you will find root causes. That means that there are almost always multiple root causes (NOT a single root cause).
Once you determine the root causes, an advanced root cause analysis system will help you go beyond root causes to find generic causes. Generic causes go beyond specific root causes to the system factors that allowed the root causes to exist.
Once you know the root causes and generic causes, you are ready to develop corrective actions. These aren’t just the common actions of discipline, training, and longer procedures. Advanced root cause analysis guides the investigation team to effective corrective actions that prevent repeat incidents.
Once you have the corrective actions approved by management (and your advanced root cause analysis system should help you get that approval), your corrective actions need to be tracked to see that they are implemented and effective.
Learning Advanced Root Cause Analysis

How can you learn about the best root cause analysis system? Start by reading about a comparison of advanced root cause analysis to 5-Whys at THIS LINK.
Register for Advanced Root Cause Analysis Training Today
If you are convinced that you need to keep your company’s performance ahead of the rapidly rising standards, you need advanced root cause analysis (the TapRooT® RCA System). The best way to learn the system is at our training. And the course that I would recommend for those that might investigate complex accidents and simple incidents is the 5-Day TapRooT® Advanced Root Cause Analysis Team Leader Training.
For more information about the 5-Day Training, CLICK HERE.
To see a list of our public 5-Day Courses being held around the world, CLICK HERE.
And to get a quote for a course at your site, CLICK HERE.
If you would like to talk to one of TapRooT® RCA Implementation Experts, call 865-539-2139.
Thanks for your interest in advanced root cause analysis, and we hope to hear from you BEFORE a major accident happens.
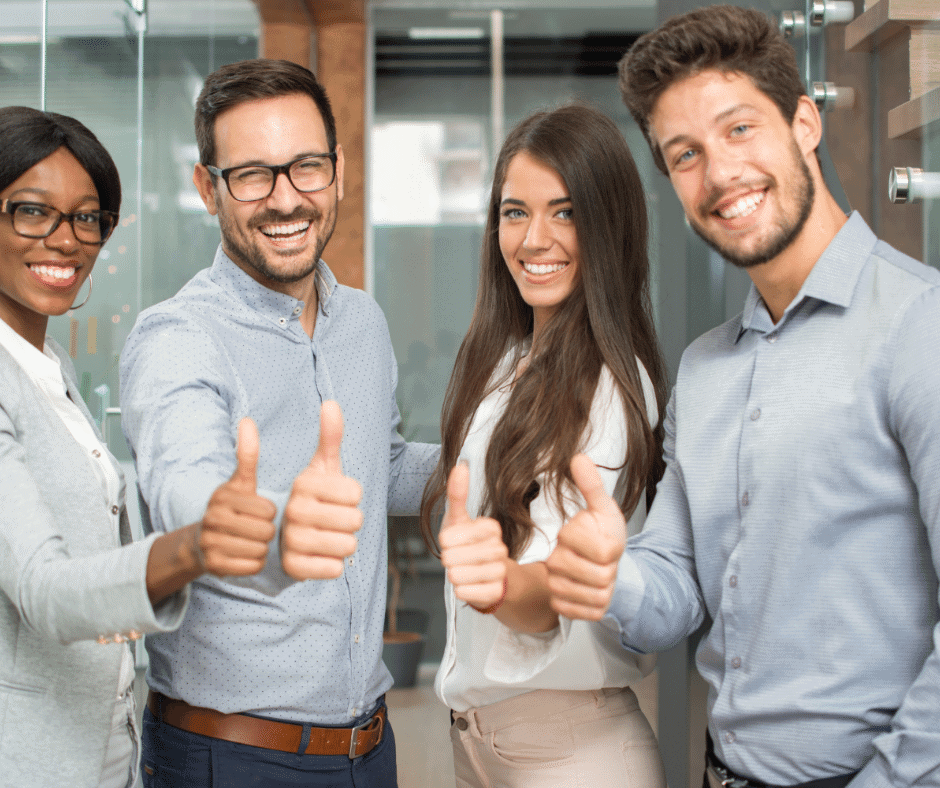