What’s in Your Plan to Stop Human Error?: A TapRooT® TV Video Premiere
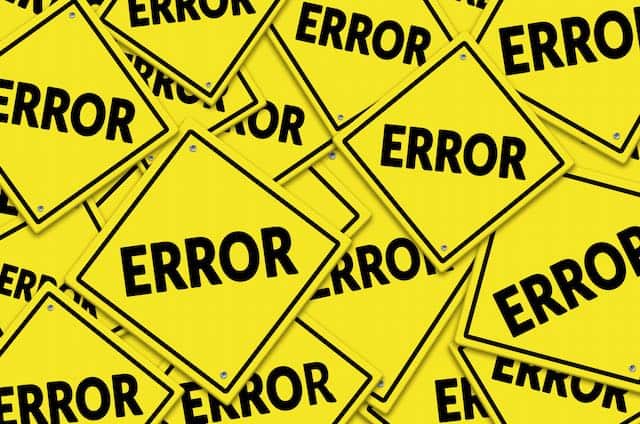
What is in your plan to stop human error? If you don’t have a plan, then consider these questions: Do you want to achieve excellent human performance? Would you like to understand the methods you can apply to effectively stop major accidents and incidents by “stopping” human error? Do you need to understand what are the most effective human performance improvement techniques and which ones are counterproductive (yes, some techniques really don’t work)?
In our Stopping Human Error course, we cover these questions and discuss hazard analysis, auditing, communication, work direction, and training. We talk about the 7 basic cause categories, and students build a plan to take back to their companies.
Watch Alex Paradies and Emily Pritt as they discuss this topic
TapRooT® TV premieres on Wednesdays at noon, on Facebook and YouTube.
You may also listen to the conversation on the TapRooT® podcast.
Develop Your Plan in the TapRooT® Stopping Human Error Course
Mark Paradies, human factors expert and Board Certified Ergonomist (certificate #85) and Alex Paradies, experienced TapRooT® Instructor and Lean Transformation leader, will help you understand:
- The causes of human error
- Human factors design best practices
- Methods to find error likely situations
- Techniques to help supervisors and workers prevent human errors
- CHAP (Critical Human Action Profile)
- Human Performance improvement Technology
- Designing your human performance improvement program.
Here is the course outline:
Course Outline
Day 1 (9:00am to 5:00pm)
- Foundations of Improving Human Performance
- Resilience and Safeguards
- Using TapRooT® Root Cause Analysis for Reactive Problem Analysis
- Using TapRooT® Human Performance Best Practices Proactively
- Human Engineering
- Procedures
- Training
- Communications
- Management System
- Work Direction
- Quality Control
- Stopping Normalization of Deviation
- Pre-Job Hazard Analysis
- Pre-Job Briefs
- Personal Safety Assessment
Day 2 (9:00am to 5:00pm)
- Applying Critical Human Action Profile Proactively
- Human Performance Improvement Technology
- Procedure Use/Adherence
- Place Keeping
- Independent Verification
- Three-Way Communication
- Pre-Job Brief
- Personal Safety Assessment
- Observation and Coaching
- Post-Job Brief
- Concurrent Verification
- Questioning Attitude
- Stop-Think-Act-Review
- Time Out
- Attention to Detail
- Management of Change
- Error Traps and Precursors
- Validate Assumptions
- Do Not Disturb Sign
- Conservative Decision Making
- Admiral Rickover and “Facing the Facts”
- Which Tools Will Work Best for You?
- Sample Plan/Suggested Plan
- Customizing Your Plan
- Present Your Plan, Benchmarking, and Feedback
With the exercises built-in to try the techniques, this is an active, quick-moving 2-day course.
You will leave this course with a clear understanding of methods to improve human performance and a custom plan to apply those methods at your company to achieve great gains in safety, quality, or operational and maintenance performance (all of which depend on human performance).
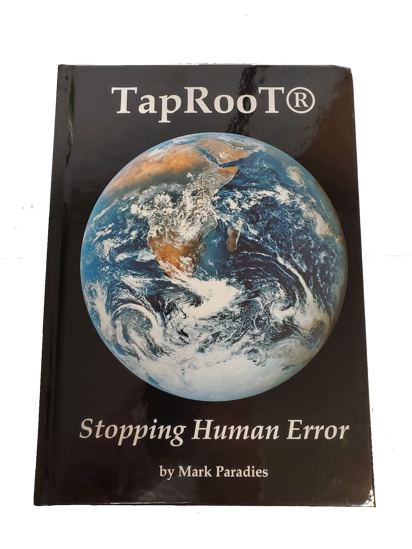
Participants receive the book, Stopping Human Error, a $99.95 value, as part of the course materials. In addition, participants receive a certificate of completion and a 90-day subscription to TapRooT® VI Software, our dynamic cloud-based software that computerizes the TapRooT® Techniques.
Find a Course near you here, or contact us about on-site training.
Continued Reading on Human Error
Join us every week for the TapRooT® TV video premiere
The premiere of new TapRooT® TV videos on Wednesdays is at noon, on Facebook and YouTube. You may also listen to the conversation on the TapRooT® podcast. Of course, you may always listen/watch at your convenience via these links, even if you miss the Wednesday premiere.
Register for a TapRooT® Root Cause Analysis Training Course
TapRooT® Root Cause Analysis Training courses are taught all over the world. If you are interested in learning how to stop repeat incidents, find a 2-day or 5-day course. We are available to train you and your staff on-site at your workplace; contact us to discuss your needs. You may also call us at 865.539.2139.