Do Tougher Penalties Improve Worker Safety?
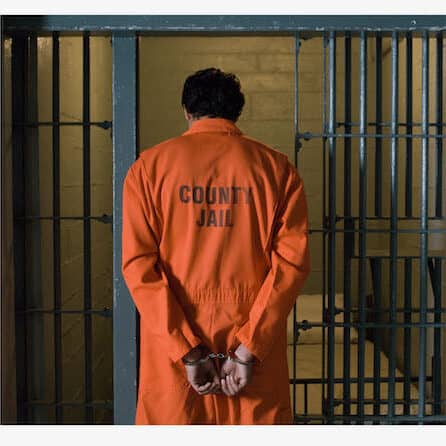
IOSH Article Implies Higher Fines May Improve Safety
In 2016 the UK implemented The Sentencing Council’s Health and Safety Offences, Corporate Manslaughter and Food Safety & Hygiene Offences Definitive Guideline. The goal of increased fines and criminal prosecutions was to improve worker safety. The Institute of Occupational Safety & Health (IOSH) wrote an article about the fifth anniversary of the law and implied that it was working.
Evidence of Effectiveness
The first evidence is that the fines handed out by the courts for accidents increased from an average of £54,000 in 2015-16, the year before the guidelines were introduced, to an average of over £150,000 in 2018-19 (although the fines fell to an average of £110,000 in 2019-20).

What about enforcement notices without court action? They fell. In 2019-2020 there were just 7,075 notices without court action – the lowest number since 2007-2008.
What about fatalities? In 2015-2016 there were 147. In 2018-2019 there were 149. In 2019-2020 there were only 111. However, the lower number in 2019-2020 was probably due to the COVID 19 lockdowns. (If we had a statistic of fatalities per hour actually worked, we would have a better idea about this.)
IOSH Conclusions

The IOSH Newsletter article quotes Ruth Wilkinson, Head of Health and Safety at IOSH, as saying:
“The average fine amount rose sharply in the first few years after the guidelines were introduced, substantially for larger organisations. We believe this, coupled with the reputational impact and worker, public and supply chain requirements for safer working practices and responsible employers, has had a significant impact in persuading businesses to invest further in looking after their workers.
“While you cannot put a value on human life, the level of fines now being handed out demonstrate and recognise society’s disapproval of serious corporate failures that lead to injury, illness and death. It reflects a desire to deter others from making the same errors and takes significant steps forward in aligning penalties for these offences with other regulatory breaches in the UK.
“We believe a strong regulatory framework, enforced properly, is persuasive in convincing businesses to invest in health and safety. However, avoiding a large fine shouldn’t be the motivation businesses require to do so. Responsible employers put looking after their staff right at the top of their priority list. This in turn has significant benefits, including a hugely reduced incident and absence rate and thus more motivated and engaged staff, leading to business benefits such as greater productivity.”
What Do You Think?
Has the increased emphasis on large fines and criminal prosecutions improved safety in the UK? Did it cause increased investment in safety improvement? Does the evidence support an emphasis on increased fines and prosecutions?
Leave your comments below with your opinions.
What Can You Do to Improve Safety?
At System Improvements, we don’t believe that increasing fines is the best way to improve health and safety. Why? Because we see little evidence that this approach works. (If you have evidence, please let me know in the comments below.)
Instead, we see quite a bit of evidence that the application of advanced root cause analysis is effective in improving safety.

Review the proof in these success stories:
- Advanced Root Cause Analysis Helps Take Lost Time Rate to Zero
- Using TapRooT® to Improve Investigations, Stop Fault Finding, Reduce Injuries, & Cut Workers’ Compensation Costs
- Improving Incident Investigations and Root Cause Analyses, and Reducing Incident Rates at Fernald
- Using TapRooT® to Reduce the Severity of Ergonomic Illnesses/Injuries & Cut Workers Comp Costs
- Improving Investigations by Focusing on Fixable Causes Rather Than Blame
- Cutting the Incident Rate and Workers’ Compensation Costs with Advanced Root Cause Analysis
All of the improvements outlined above were accomplished without increased fines. Nobody went to jail. Instead, they learned to apply TapRooT® Root Cause Analysis to improve safety and reduce workers’ comp costs.

Would your management be more likely to tackle improving your root cause analysis to improve safety, reduce injuries, save on workers’ comp costs, and avoid fatalities, OR would they be more likely to be motivated by the threat of fines and jail time if they have a major accident?
Again, let me know what you think would work better for your management in the comments section below.
And if you would like to discuss implementing advanced root cause analysis, getting a “Management Briefing” and developing a “Roadmap for Success,” and, perhaps, even scheduling advanced root cause analysis training, call us at 865-539-2139 or CLICK HERE to contact one of our implementation experts.
Clinton Wiggins replied…
It’s ALWAYS better to drill down to the Root Cause, learn from it, fix it, and educate all stakeholders about it, so it’s not repeated.
Only the “truly ignorant” would believe that increasing fines improves (and sustains?) Safety. I say “truly ignorant” not to demean, but to amplify the fact of their confirmation bias of What You Look For Is What You Find – WYLFIWYF… kind of like the carpenter who mainly uses a hammer, so that is his instrument of default, at least for trial & error….
Just as most default to cognitive biases of blaming people for being stupid when they make a mistake, it is also simply more cognitive biases to blaming management and executive leadership for not caring enough and not being engaged enough to ensure a strong(er) culture of safety, when a worker experiences a SIF event.
Remember that BP executives helicoptered out to the rig to acknowledge Transocean’s safety record before the Deepwater Horizon event in the Gulf of Mexico. How does that translate into not being engaged and not caring enough to be personally involved? Clearly, it does not match up at all.
Nonetheless, regulatory agencies miss the point that the reason employee engagement and leadership involvement appear lacking are the evident problems not the underlying or root causes.
An underlying cause of an insufficiently functioning safety culture that is not effectively promoting and sustaining a cultural imperative for intolerable risk is the absence of everyone having fundamental safety responsibilities. Regulatory bodies (and most others) keep trying to surround the “evident problems” with a solution, because they lack depth in their understanding, not realizing that role definition and shared accountability are what cement a just – fair – strong organizational sub-culture for safety and health.
A fine and root cause are not at opposite ends of the seesaw. If a company is financially focused small fines are just a cost of business. Fines, big or small ,impact the bottom line are going to have solutions developed, communications etc. A SIF is a bad day for a company, a bad day that moves farther and farther into the past. SIF’s are events that happen to other employees. Besides does knowing the root cause to the Nth level really matter for an incident? Add a line to the training, add a guardrail, buy sparkless tools. Changing the input will change the output. If regulation does not allow for firing the employee then terminate the boss. There are lots of low cost easy options. In this culture of shorter spans at a single company there is not as much vested interest in each other. Why spend the effort to know with absolute certainty what the root cause is? For 20% of the effort 80% of the solution can be had with fishguess diagrams. A cheap effective method of finding things to change. Think of the daycare that implemented fines for late parents. Once the parents knew the cost they were late more often. Not many leaderships are going to follow the lead of Alcoa and change the culture. They are not going to make that change based on a potential fine.
Unless the fine is for not using programs as effective as taproot companies are not going to choose a deep dive safety system based on the level of the fine.
Theoretically, one might think that higher fines would encourage companies to make positive changes to improve safety and ultimately, avoid higher fines. But in reality, it could also keep companies from reporting incidents and when incidents don’t get reported, the hazards in the work place go unaddressed. If you look at the death rate numbers (and I feel that the 2019-2020 numbers are an outlier due to COVID), in theory, we should have seen a drop in deaths (147 in 2015-16 and 149 in 2018-19) but instead, we saw an increase. The death rates may indicate that companies started not reporting and not addressing safety issues. I don’t believe higher fines helps to increase worker safety, in fact, it may have the opposite effect.
Typical governmental response is to tax and fine your way out of every problem… Just like penalty-based safety programs, it does not address the root cause but serves to drive the issue underground. Sadly, not a surprise.
I think the correct answer to the question is “It depends.” One of the main tenants of root cause analysis is that people do not go to work thinking “I am going to make a mistake today.” In other words workers usually try to do the right thing, so we look for other “human factors” issues which contributed to the mistake. We don’t usually blame the individual unless they willfully violated a safety barrier, knowing the consequences of their action. Even then, if what they did was a common practice among their co-workers, we then look at why it was a common practice, and again take the focus away from the worker. This encourages people to report when they have made an honest mistake, so we can look at precursors to major events, and put barriers in place before a major event happens.
If management, or a specific manager, discourages reporting, and looks the other way when minor events happen, then that individual does bear responsibility. This is a case where blame is appropriate for the entire management team, or at least for an individual.
In the US the Nuclear Regulatory Agency has a policy that Nuclear Utilities must create a Safety Conscious Work Environment (SCWE). Individuals are encouraged to report issues, and must have multiple pathways for reporting issues (supervisor, manager, manager’s boss, independent anonymous organization, directly to the NRC).If there is a major issue at a US nuclear power plant, the NRC will look at the corrective action program, as well as who knew about precursors, what they did about it (if anything), follow-up actions taken to ensure corrective measures were implemented, and the effectiveness of the corrective measures. In other words, they look at the whole root cause action plan from start to finish. In this case, fines and imprisonment may be appropriate if the root cause process was purposefully corrupted. The whole SCWE process has been required of the entire nuclear industry, and as far as I have seen, has been fairly effective. Not only in decreasing injuries, but also in helping the industry perform better. Average capacity factor for nuclear power plants in the US is now above 95%.
I think the correct answer to the question is “It depends.” One of the main tenants of root cause analysis is that people do not go to work thinking “I am going to make a mistake today.” In other words workers usually try to do the right thing, so we look for other “human factors” issues which contributed to the mistake. We don’t usually blame the individual unless they willfully violated a safety barrier, knowing the consequences of their action. Even then, if what they did was a common practice among their co-workers, we then look at why it was a common practice, and again take the focus away from the worker. This encourages people to report when they have made an honest mistake, so we can look at precursors to major events, and put barriers in place before a major event happens. If an honest mistake occurs (our basic assumption), then fines and imprisonment are not appropriate to improve worker safety.
If management, or a specific manager, discourages reporting, and looks the other way when minor events happen, then that individual does bear responsibility. This is a case where blame is appropriate for the entire management team, or at least for an individual.
In the US the Nuclear Regulatory Agency has a policy that Nuclear Utilities must create a Safety Conscious Work Environment (SCWE). Individuals are encouraged to report issues, and must have multiple pathways for reporting issues (supervisor, manager, manager’s boss, independent anonymous organization, directly to the NRC).If there is a major issue at a US nuclear power plant, the NRC will look at the corrective action program, as well as who knew about precursors, what they did about it (if anything), follow-up actions taken to ensure corrective measures were implemented, and the effectiveness of the corrective measures. In other words, they look at the whole root cause action plan from start to finish. In this case, fines and imprisonment may be appropriate if the root cause process was purposefully corrupted. The whole SCWE process has been required of the entire nuclear industry, and as far as I have seen, has been fairly effective. Not only in decreasing injuries, but also in helping the industry perform better. Average capacity factor for nuclear power plants in the US is now above 95%.