How do you stop a major incident before it happens?

Q. How can you isolate & investigate the problems that may lead to a major incident before it happens?
A. Use Advanced TapRooT® RCA to fix the root causes of the precursor (not a major incident; more later on this) that warn you of impending failures.
You may ask, How can Advanced TapRooT® RCA (root cause analysis) prevent a major incident before it happens?
The short answer is, Advanced TapRooT® RCA is designed for the express purpose: to stop a major incident prior to it happening. You know, the type of major incident none of us wants to have happen or to have to investigate, such as:
- Incidents involving a fatality,
- Major environmental damage,
- Serious injury,
- Major quality issue or product recall,
- a regulatory issue, or
- Serious production outage.
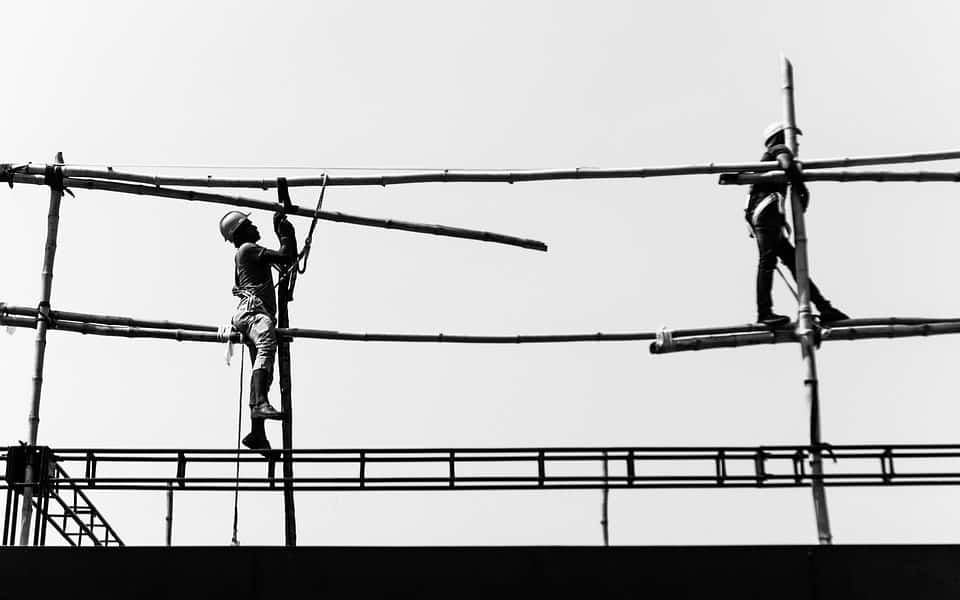
TapRooT® Co-founder, CEO, and President of System Improvements Mark Paradies comments, “I’ve never seen a major accident that didn’t have several—perhaps up to a dozen—precursor incidents that could have been investigated and used to solve the problems and, thereby, to stop the major accident.”
Paradies asks and answers, “Why do major accidents happen? Because people ignore the warning signs.”
He explains, “They don’t invest the effort—or they don’t have the knowledge—to find the root causes of the problems and fix them before the next major accident occurs. That’s why we developed the TapRooT® Root Cause Analysis System: To help people go beyond their current knowledge to find and fix the root causes of incidents. TapRooT® helps companies learn from their experiences and prevent major accidents.”

Enter Book 4: TapRooT® Root Cause Analysis for Major Investigations
Book 4, TapRooT® Root Cause Analysis for Major Investigations, in the TapRooT® Root Cause Analysis Training System, equips you to learn to do investigations for major incidents as fast and easy as possible with credible results and effective corrective actions.
TapRooT® Root Cause Analysis for Major Investigations takes the user through an in-depth look at the techniques used to perform a TapRooT® Investigation. Completing the book set are the Root Cause Tree®, Root Cause Tree® Dictionary, and Corrective Action Helper®.
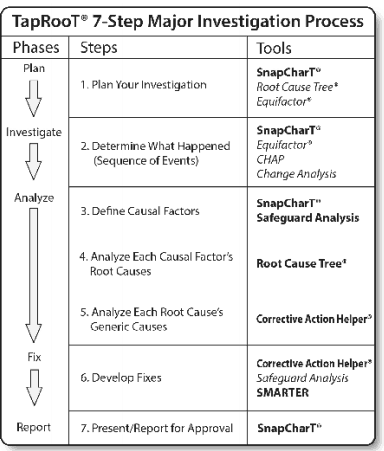
Peruse the Book 4 table of contents below for further insights into the education and expertise you will gain from this unique resource:
Chapter 1: Major Investigations vs Basic Investigations
Chapter 2: The TapRooT® 7-Step Major Investigation Process
Chapter 3: Step 1: Plan Your Investigation
Chapter 4: Step 2: Determine What Happened
Chapter 5: Step 3: Define Causal factors
Chapter 6: Step 4: Analyze Each Causal Factor’s Root Causes
Chapter 7: Step 5: Analyze Each Root Cause’s Generic Causes
Chapter 8: Step 6: Develop Fixes
Chapter 9: Step 7: Present/Report for Approval
Get your feet wet: Sample a snippet of the book before you attend the course
In the first chapter of the book, Using TapRooT® Root Cause Analysis for Major Investigations, co-author Mark Paradies underscores the unfortunate truth: “Major accidents aren’t caused by nice, tidy, simple, easy-to-fix problems. Therefore, management won’t be happy with your investigation. Thus, your job will be a difficult one.
“You must discover the causes of a perhaps complex, difficult-to-solve problems, develop effective fixes, and then present what you have learned to management in such a clear, unambiguous way that they understand the problems and the solutions. They must leave the meeting convinced that they need to change the way they are managing the company and lead the change that needs to happen.
“The first part of this difficult task is for you, the investigator, to understand what happened, the Causal Factors, the root and generic causes, and the fixes that will prevent future problems. This is predominantly what the TapRooT® System is about. This is what you will learn in the 5-Day TapRooT® Advanced Root Cause Analysis Course.”*
*Using TapRooT® Root Cause Analysis to Investigate Precursor Incidents and Major Accidents: A White Paper by Mark Paradies.
Changing the Way the World Solves Problems . . . this is what the TapRooT® System is all about
The TapRooT® System provides people the science to find and fix the causes of human error and equipment failure—whether it is reactively stopping low to medium risk incidents or investigating major accidents (the topic of this book); or proactively improving performance by using the TapRooT® Techniques to find and fix a problem’s root causes before an accident occurs.
Mark Paradies and Linda Unger created the TapRooT® System because they saw people trying to solve problems without understanding the problem’s root causes. They observed that:
- Most people investigating incidents don’t have training in human factors and cannot see the root causes of human errors.
- Many others address only the symptoms of equipment problems without accurate troubleshooting and root cause analysis of the reliability issue.
It took Paradies and Unger more than a decade to develop a system that addressed both issues. But they didn’t stop. Together with the staff at System Improvements and client users in the field, they continued to improve the TapRooT® System to make it the world leader in performance improvement technology.
Get started — Actualize your resolve that will be no major accidents on your watch
To get started, order Book 4. You may also want to enroll yourself or your team in the 5-Day TapRooT® Advanced Root Cause Analysis Team Leader Training Course, offered in locations around the globe or on-site at your facility. Call us (865.539.2139) to discuss a location or inquire further about TapRooT® Root Cause Analysis Training. We’re here to find solutions for you.
Announcing the newest TapRooT® RCA offerings: Book 10 and the Complete TapRooT® 10-Book Set
We recently completed the latest book in the TapRooT® Root Cause Analysis book series, Book 10, Stopping Human Error. Subsequently, we have produced the first-ever set of the entire TapRooT® book series (order it today from the store).