Unstable Approach, Failure to Go-Around Leads to Hard Landing (Bad Day)
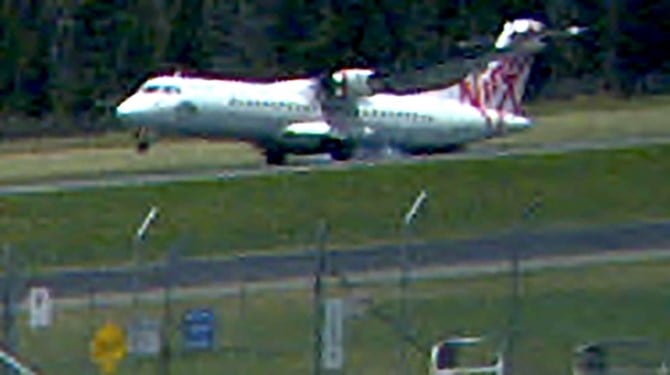
The Australian Transport Safety Board (ATSB) highlights the importance of adhering to standard operating procedures (SOP) following the release of a final investigation report regarding the hard landing of an ATR 72 airliner, resulting from an unstable approach.
On November 10, 2017, ATR 72-212A VH-FVZ operating as Virgin Australia flight VA646 was readying for landing at Canberra Airport in conditions of light turbulence. On the flight deck were the captain (who was also a training captain), the first officer (who the captain had previously trained), and a check captain. The check captain was conducting a routine annual operational line check of the captain and a six-month operational line check of the first officer over four flights on the day. The occurrence flight was the last of these flights. In the main cabin were two cabin crew members and 67 passengers.
During the landing approach, the first officer, who was the pilot flying, assessed that the aircraft was overshooting the desired approach profile. In response, at a height of 118 feet above the runway, he reduced engine power to idle, but this resulted in an abnormally high descent rate (in turboprop aircraft, large propellers spinning rapidly in low pitch create a significant increase in drag).
The aircraft captain, who was the pilot monitoring, identified that power was incorrectly set and called twice for an increase in power before subsequently intervening and increasing power himself. This intervention, however, occurred too late to arrest the high rate of descent.
Four seconds prior to touching down, the aircraft was descending at a rate of 784 feet/minute, already greater than the design limit of the undercarriage and above the normal descent rate for the approach of about 575 feet per minute. At that time, the aircraft was subjected to a significant change in the wind from a 10 knot headwind component to a 2 knot tailwind component. This resulted in a further loss of lift, and the captain later stated that he felt the aircraft drop out from under him.
Consequently the aircraft reached a recorded 928 feet per minute descent rate at touchdown, resulting in a 2.97 G hard landing on the main landing gear, tail skid, and underside of the rear fuselage, incurring substantial damage.
“Unstable approaches continue to be a leading contributor to approach and landing accidents and runway excursions.”
The aircraft subsequently required inspection of landing gear components, reskinning of sections of the fuselage underside, and replacement of the tail skid and a drain deflector mast before it could return to service.
“The continuation of the approach when a go-around should have been conducted allowed the subsequent conditions to develop, leading to the hard landing,” ATSB Executive Director Transport Safety Nat Nagy said.
“This occurrence demonstrates the importance of crews adhering to standard operating procedures and conducting a go-around when an approach becomes unstable.
“It also highlights the risks associated with incorrect handling of an approach to land, and the need for prompt and decisive action, as the available time to remedy an unstable approach situation is short.”
Mr. Nagy noted that unstable approaches continue to be a leading contributor to approach and landing accidents and runway excursions.
Safety message from the investigation
Unstable approaches continue to be a leading contributor to approach and landing accidents and runway excursions. This occurrence demonstrates the importance of crews adhering to standard operating procedures and conducting a go-around when an approach becomes unstable. It also highlights the risks associated with the incorrect handling of an approach to land and the need for prompt and decisive action as the available time to remedy the situation is limited.
Read the ATSB’s further findings in the investigation report.
Equifactor® Equipment Troubleshooting and TapRooT® Root Cause Analysis Training
Do you need to efficiently and effectively find the root causes of equipment failures to improve your facility’s equipment reliability? Imagine the downtime prevented, and money saved NOT having repeat equipment failures. If this sounds interesting (and worthwhile), then this completely revised TapRooT´® Equifactor® course is for you.
The Equifactor® Techniques are based on the work of noted equipment reliability expert Heinz Bloch. The tools can be used by maintenance personnel, equipment reliability specialists, maintenance managers, or investigators who don’t have an extensive understanding of equipment engineering.