Will You Stop Doing Root Cause Analysis? (Because of the EPA’s RMP Revisions)
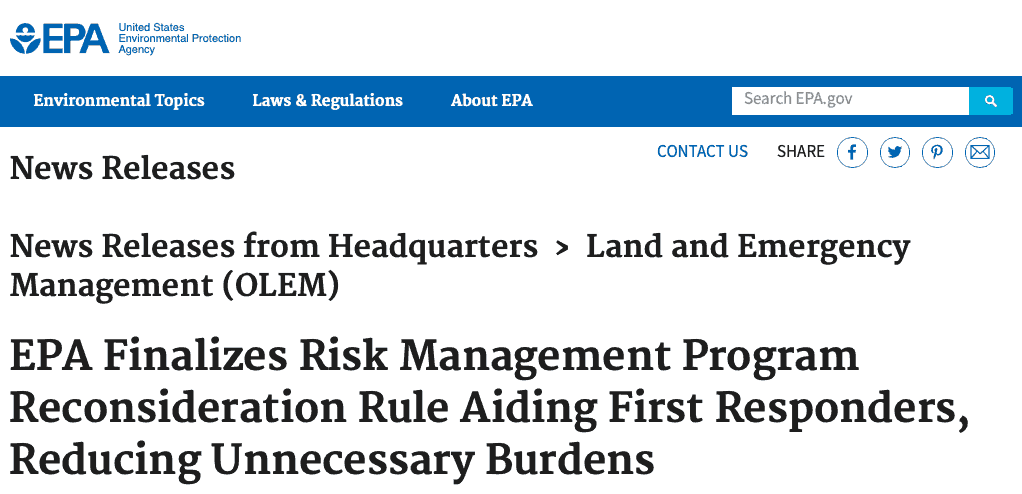
EPA Revises RMP Rule Revision –
Removes Requirement for Root Cause Analysis
On November 21, the EPA released the final Risk Management Program (RMP) Reconsideration Final Rule (click HERE for details). I am late to the party concerning the revisions to the EPA’s Risk Management Plan. I guess you could say I was ambivalent to the whole discussion about adding or subtracting the words “root cause analysis” to the RMP section on incident investigation.
With my background in root cause analysis and my efforts to get people to perform advanced root cause analysis, you might ask: “Why I am ambivalent?” The answer is simple. I don’t think that good management can be mandated. And quite simply, good management is what advanced root cause analysis is all about.
The way the new (2017) regulation was written, people would have to identify root causes using a “recognized method.” The EPA defined a root cause as:
A fundamental, underlying, system-related reason why an incident occurred.
That isn’t quite our definition (see our definition HERE), but it is close enough.
I know the people who wrote the regulation and I know they would have liked to say a recognized method like TapRooT®. But you can’t say that in a regulation. So, weaker wording was used. Wording that could include almost anything (even 5-Whys).
Thus, the new regulation probably would not have improved the industry’s incident investigation and root cause analysis.
Good Management
I think that any well-managed process safety management program would include root cause analysis of process safety-related accidents and incidents (near-misses). The good programs use TapRooT®. So, well-managed companies don’t need a regulation to tell them about the advantages of advanced root cause analysis.
And what about companies with poor process safety management programs? The changes in the regulation of adding “root cause analysis” and a “recognized method” to the incident investigation portion of the regulation would not require them to actually perform improved root cause analysis. A poor root cause system could be “recognized” by their management and probably be “good enough” under the 2017 regulation proposal. Thus, bad management would still be bad management with bad root cause analysis. No improvement achieved.
Cost of Root Cause Analysis
There was one part of the current revision to the 2017 regulation proposal that I objected to. One of the objections to the change was the cost of implementing the new portions of the regulation. Someone decided that the industry could save $1.8 million per year by not doing root cause analysis. I think this cost estimate is ridiculous.
First, most good companies already perform a root cause analysis on process safety-related incidents. Therefore, the cost for these companies is ZERO.
As for poorly managed companies that don’t use root cause analysis, they could discover the power of root cause analysis and how much money they could save.
Therefore, the net result would be money saved, not a $1.8 million dollar cost.
And even if the cost was $1.8 million across the industry, with 12,542 facilities affected by the regulation, the cost is only $144 per facility per year. That’s almost nothing when you consider the value received when you fix problems effectively.
Will You Stop Performing Root Cause Analysis?
I don’t think anyone using TapRooT® will stop performing root cause analysis just because the EPA didn’t require it in the revised regulation.
I hope people who aren’t performing effective root cause analysis will reconsider and have a look at an advanced root cause analysis system – TapRooT® – and start applying it to prevent major process safety accidents BEFORE they happen.
Would you like to see some success stories to see what implementing TapRooT® has done for other sites/companies? Then read these:
Chemical Company Reliability Example
Another Chemical Industry Example
Or watch one of these video success stories…
Find Out What You Should Be Doing
To find out more about TapRooT® Root Cause Analysis, see:
https://www.taproot.com/about/
To learn about TapRooT® Software, see:
https://www.taproot.com/solutions/software/
To learn about the various TapRooT® Training, see:
https://www.taproot.com/solutions/rootcausetraining/
And see our public TapRooT® Course schedule at:
https://www.taproot.com/store/Courses/
Attend the 2020 Global TapRooT® Summit and learn the latest improvements to TapRooT® Root Cause Analysis. See the Summit schedule at:
https://summit.taproot.com/schedule
Or download the brochure by clicking on the image below…
What a headline! “US Administration guts Chemical Disaster Rule adopted after fatal 2013 Texas fertiliser explosion”
I can’t believe we are writing about the same rule change. See: http://www.hazardexonthenet.net/article/175947/US-Administration-guts-Chemical-Disaster-Rule-adopted-after-fatal-2013-Texas-fertiliser-explosion.aspx
They didn’t mention that the new rules would do nothing to prevent an accident like the West, TX, explosion since it was found to be caused by arson.