Monday Accidents & Lessons Learned: How Are You Protecting Excavator Workers?
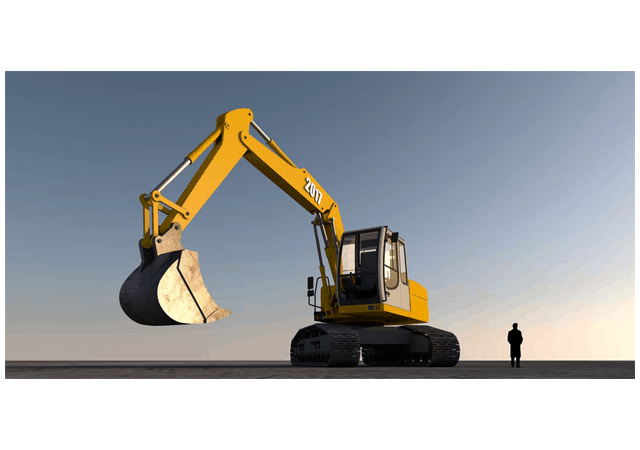
The Department of Mines, Industry Regulation, and Safety in Western Australia recently issued a safety alert about contact with workers or equipment by excavators, following a number of incidents.
Incident Background
Since 2015, two workers have been seriously injured through contact with an excavator while it was being utilized as a crane. In both instances, the controls for the bucket, boom, or dipper arm of the excavator were inadvertently or incorrectly activated while the workers were within the slew radius (slewing: trapping a person between the excavator and a fixed structure or vehicle). Additionally, there have been three reported incidents of personnel working within the slew radius of an operating excavator and, having entered the working radius, were damaged by contact with the excavator.
Summary of hazard
The unintended movement of the bucket, boom, or dipper arm on an excavator can result in:
- a serious or fatal injury
- instability of the excavator
- damage to equipment
Contributory factors
- Inadequate communication with mobile plant operators
- Workers and vehicles in the line of fire of an operating excavator
- Failure to follow the original equipment manufacturer’s (OEM’s) operating instructions, including application of the hydraulic lockout lever to lock the controls and prevent inadvertent movement of the bucket, boom, or dipper arm
Safe work Recommendations
The following actions were recommended to managers, supervisors, and operators to reduce the potential for an excavator making inadvertent contact with workers or equipment.
- Confirm workers are competent to use the equipment and perform the work activities.
- Confirm adequate hazard identification and risk management has been conducted prior to undertaking work.
- Provide a means of direct positive communication (e.g. radio) for workers on foot to communicate with the equipment operator if they are required to enter the working radius of the machine.
- Ground the bucket (where practicable) prior to any workers entering the slew radius of the excavator.
- Apply the hydraulic lockout lever when workers need to enter the slew radius of the excavator to carry out work.
Fit-for-purpose equipment
If an excavator is being utilized as a crane to lift a freely suspended load, then the excavator must comply with the requirements of Section 5 of the Australian Standard AS 1418.8 Cranes, hoists, and winches – Special Purpose Appliances, and be operated within the OEM’s specifications (e.g. swing radius should be demarcated).
Further information
- Standards Australia, www.standards.org.au
AS 1418.8 Cranes, hoists and winches – Special purpose appliances - Department of Mines, Industry Regulation, and Safety, Mines safety alerts, www.dmp.wa.gov.au/Safety/Mines-safety-alerts-13194.aspx
- Mines Safety Bulletin No. 114 Compliance requirements for multi-purpose mobile plant
- Mines Safety Bulletin No. 143 Use of an excavator bucket as a lifting point
Reviewing Australian excavator incidents and safety alerts, TapRooT® found a fatal excavator incident in New South Wales (NSW) in which the death precipitated an entitlement compensation for the victim’s workplace injury in addition to the death benefit, and another case of death resulting from an excavator injury in which the NSW company was fined $300,000 and its director an additional $60,000.
The Australian Minister responsible for SafeWork NSW, Matt Kean, called the penalty a warning to businesses and bosses. “This awful death is a stark reminder of the responsibilities employers have to make sure they provide a safe workplace,” he said. “At this business, the risk of workers coming into contact with the excavator while sorting waste was significant, and the business should have had safe work systems to prevent it.”
Kean underscored that the investigation exposed that there was no traffic management plan or exclusion zone to separate workers from the excavator, and no means for sorters to communicate with the excavator operator.
“Workers had received no training on the need for an exclusion zone around the excavator, and no supervisor had been appointed to enforce an exclusion zone,” he said.
That these incidents involving worker injuries and fatalities continue to occur (for example, between 1992-2000, there were 346 deaths caused by excavators or backhoe loaders in the United States) highlights the critical need for companies to prioritize and actualize safety in the workplace. Some valuable excavator-specific guidelines are given here and here.
Watch TapRooT’s Emergency Scene Management: How to Prioritize Actions during an Investigation to learn crucial protocol criteria, including preplanning to mitigate hazards at the scene of an incident, situational awareness, emergency services, and more critical actions that you need to perform in incident response.
Get Barb Carr’s book, TapRooT® for Evidence Gathering and Interviewing, at our website, and contact us to enroll in a course, such as 2-Day Effective Interviewing & Evidence Collection. The course is also being offered at our 2019 Global TapRooT® Summit (contact us if you would like to enroll in this course). See which Pre-Summit Courses would be most helpful to you:
- TapRooT® Root Cause Analysis Training
- Equifactor® Equipment Troubleshooting and Root Cause Analysis
- Trending to Manage Performance
- TapRooT® Analyzing and Fixing Safety Culture Issues
- Risk Management – Best Practices & Risk-Based Thinking
- TapRooT® Software Implementation & Application
- “What if” and TapRooT® for Hazard Assessment
- TapRooT® Evidence Collection and Interviewing Techniques to Sharpen Investigation Skills
- Stopping Human Error
- Mistake-Proofing & Effective Corrective Actions
- Advanced Causal Factor Analysis