Problems using 5-Whys? Read “Under Scrutiny” from Quality Progress to Understand Why!
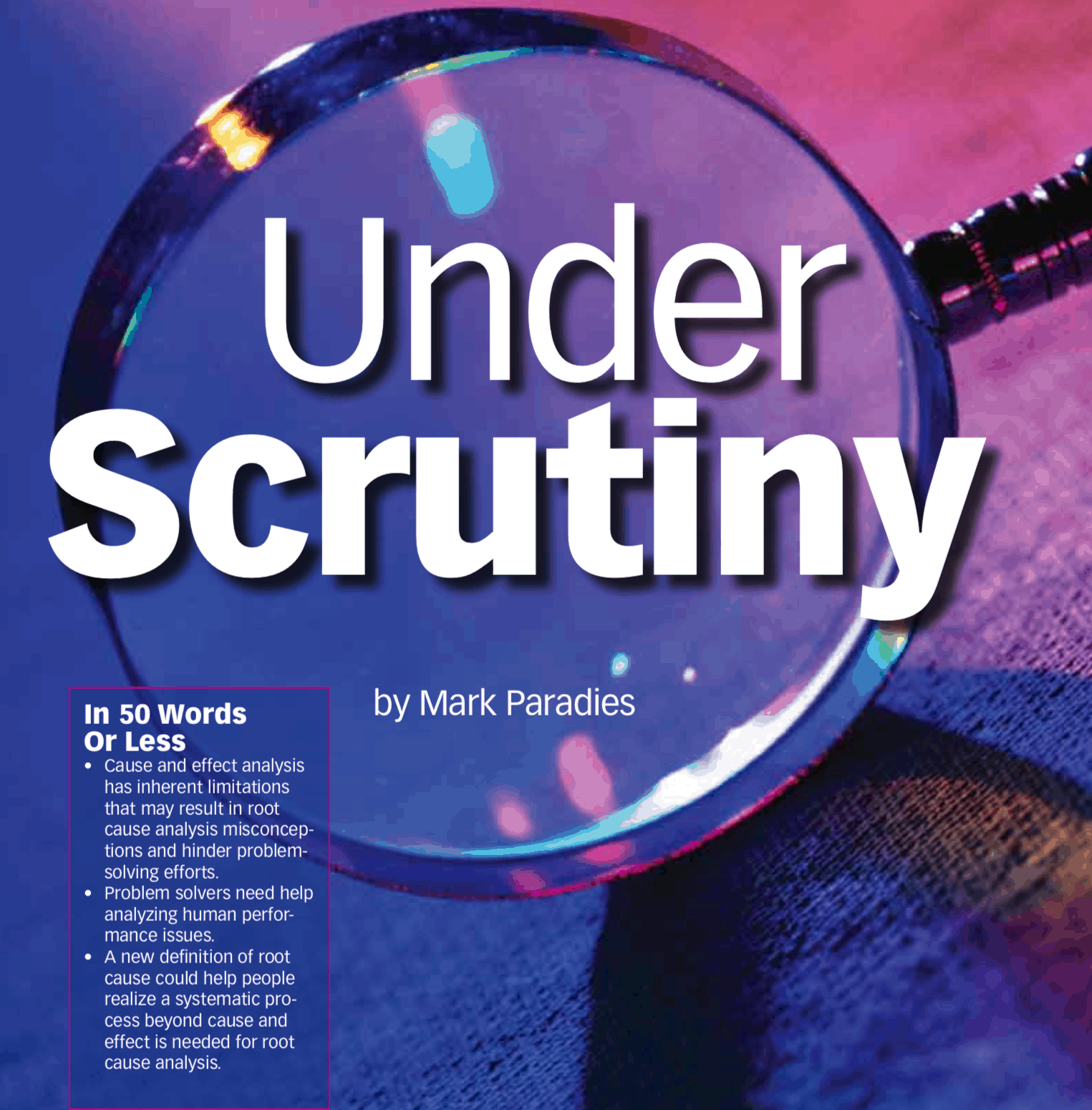
Root Cause Analysis Under Scrutiny
Are your root cause analysis results “under scrutiny?” Do you have problems finding the root causes of quality problems, safety incidents, or mechanical failures? It could be because of the root cause analysis tools you use. Some tools have inherent weaknesses that are “built-in.” You will always have problems when faults are built-in to the tools you use.
The article (“Under Scrutiny” – used here by permission – reprinted from Quality Progress, the flagship magazine of the quality professional society ASQ), explains why some techniques commonly recommended for root cause analysis (like 5-Whys) will cause problems when applied to find root causes. Read the article at the link below:
Under Scrutiny article from Quality Progress
Read More…

But there is even more wrong with the 5-Why example in the Quality Progress article.
First, you can read about the “debunking” of the article at THIS LINK.
It seems that instead of asking 5-Whys, they spent over $2,000,000 finding causes of the monument’s problems.
Plus, you can read more about the limitations of 5-Whys at this link:
What can you do to overcome the limitations inherent in 5-Whys? Stop being “under scrutiny” and try something new. Something built on a solid foundation of human factors and root cause analysis research.
Time to try something new…
Once you finished reading about the limitations of 5-Whys and Cause-and-Effect, sign up to learn about the advanced root cause analysis system that was intelligently designed to avoid those problems … TapRooT®.
Use the link at the bottom of the page to sign up for our weekly root cause analysis newsletter. CLICK HERE to see our TapRooT® TV YouTube page and subscribe (make sure you click the notification bell).
CLICK HERE for more information about TapRooT® (including a TV interview of Mark Paradies about root cause analysis) and HERE for information about TapRooT® Root Cause Analysis Training.
Don’t continue to suffer through the limitations of 5-Whys and Cause-and-Effect. Learn a better system that was designed to get to the bottom of human performance and equipment reliability issues – TapRooT® Root Cause Analysis.